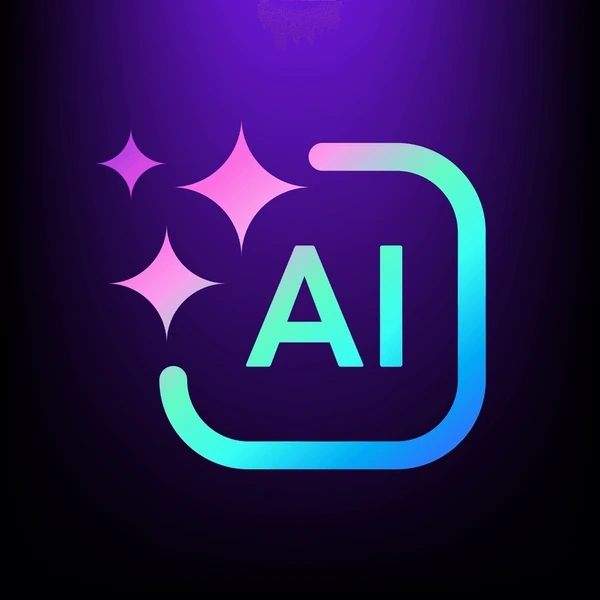
Smarter email, faster business.
How to Use Digital Twins for Predictive Maintenance in Aviation
July 08, 2025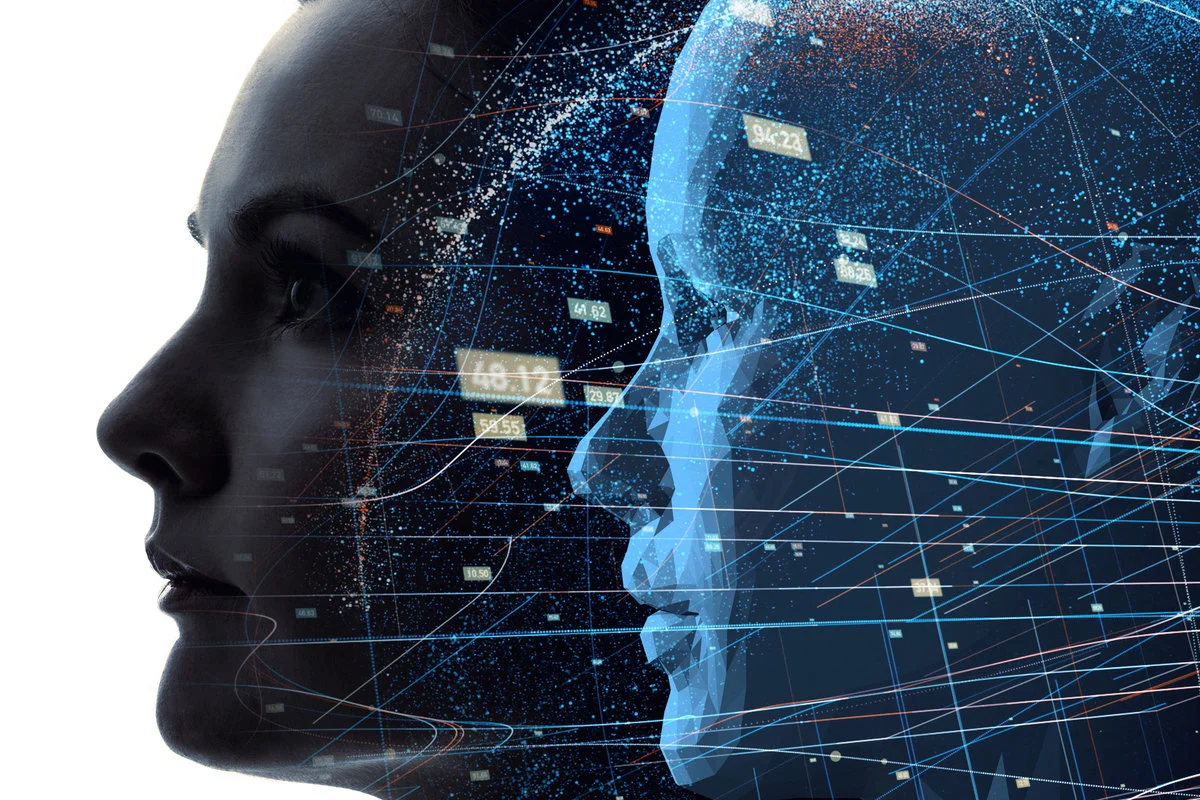
Digital twins are here, helping airlines slash downtime, cut maintenance costs, and boost safety. Here’s how predictive maintenance is taking off in aerospace innovation.
In aviation, even a single unscheduled delay can trigger a costly chain reaction—grounded flights, rerouted aircraft, disrupted crews, and unhappy passengers. The industry runs on precision, but traditional maintenance methods with routine checks, calendar-based overhauls, and reactive repairs often lag behind the demands of modern air travel.
Digital twin predictive maintenance may be the cure. The technology brings a powerful method for airlines and OEMs to foresee failures before they happen, using real-time data and virtual models of aircraft systems.
With digital twins, fleet MRO teams can mirror existing physical assets with digital counterparts. Then, they put the virtual twin through a range of stress tests, including severe weather, component failure, and response to unplanned downtime. This proactive approach extends aircraft life and improves operational workflows and flight safety.
This added precision is critical for an industry that’s built on tight margins and tighter regulations.
What are digital twins?
The idea behind digital twins was born in the early 2000s, but its roots stretch back to NASA’s 1970 Apollo 13 mission (Siemens).
During the crisis, NASA engineers used mirrored systems on Earth to simulate the failing spacecraft in real time in a primitive version of what we now call a digital twin. The formal concept was first defined in 2002 by Dr. Michael Grieves at the University of Michigan, in the context of product lifecycle management (Digital Twin Open Research Platform).
At its core, a digital twin is a dynamic virtual model of a physical object, process, or system. Unlike a static simulation, a digital twin is continuously updated with real-world data via sensors, machine learning models, and networked systems. This allows it not mirror real-world conditions, and also to simulate, predict, and optimize the performance of its real-world counterpart.
Today, digital twins are used far beyond aerospace. In manufacturing, Siemens uses digital twins to simulate factory layouts and machine efficiency. In automotive, Tesla and BMW leverage twins to monitor electric vehicle performance and improve autonomous driving systems. Healthcare is applying the tech to simulate organs and predict how individual patients might respond to treatments (Deloitte).
Urban planners now use digital twins to model entire cities. Singapore’s Virtual Singapore project is a living digital replica of the city-state, used for urban planning, emergency response, and environmental analysis (Observatory of Public Sector Innovation). Meanwhile, energy companies like GE and Shell employ digital twins to manage turbines, power grids, and offshore rigs in real time (GE Vernova, Shell).
These use cases are made possible thanks to advances in IoT, cloud computing, and edge analytics. As 5G connectivity and AI modeling evolve, the scope of digital twins is expanding rapidly—bringing real-time optimization and scenario testing to industries once limited by lagging data and manual oversight.
What is a digital twin in aviation?
A digital twin is a virtual replica of a real-world object, system, or process that reflects its current state using live data. Unlike static models or other simulations, a true digital twin is linked to its physical counterpart and updates continuously based on inputs from sensors and its operational environments (Lufthansa Systems).
There are multiple types of digital twins used in aviation:
- Component twins (e.g., engines or landing gear)
- System twins (e.g., avionics or hydraulics),
- Process twins (e.g., baggage handling or ground servicing)
- Aircraft-level or fleet twins that integrate all subsystems into a cohesive digital model
Boeing, for instance, uses digital threads and twins to track the performance of critical systems in programs like the MQ-25 and Chinook. Their approach creates a “closed-loop” connection between design and operation, where real-world usage informs future engineering iterations (Boeing Innovation Quarterly).
This level of fidelity allows aviation stakeholders not just to monitor assets, but to simulate how those assets will behave in future scenarios, from structural fatigue cycles to emergency reroutes. As Lufthansa Industry Solutions puts it, “The ‘Digital Twin’ enables companies to map their processes virtually, make changes, and, in doing so, tap into real potential for optimization” (Lufthansa Systems).
Why “digital twins” and not “triplets” or “quadruplets”?
If a digital twin can simulate real-world conditions, why stop at one? Why not create three or ten or fifty versions of the same system to test every possible outcome?
We’re already there. Many systems already do just that.
The term digital twin originally came from NASA in the early 2000s, when engineers needed a virtual model of spacecraft that could run in parallel with the physical version in space (NASA). The idea was to build a one-to-one digital replica that continuously reflects the real system’s status.
Since then, the concept has evolved. Today’s digital twins often use scenario modeling or Monte Carlo simulations, techniques that run hundreds or thousands of simulated futures to evaluate best-case, worst-case, and most likely outcomes (NASA Ames Research Center). In aviation, for example, predictive maintenance models might test different environmental conditions or usage patterns to forecast when a component is likely to fail (Electric Power Systems Research).
So why don’t we call them digital triplets or digital multiples?
It comes down to branding and simplicity. Digital twin became the catch-all term because it’s easy to grasp and widely recognized across industries. Even if an engine or airframe has 10 parallel simulations running in real time, the whole system is still referred to as “the digital twin” for consistency. It keeps the language clean for engineers, executives, regulators, and marketers alike (McKinsey & Company).
Yes, digital twins often behave like entire digital families, but the term twin stuck persists even if it doesn’t tell the whole story.
How predictive maintenance works with digital twins
Traditional maintenance relies on fixed schedules like 500-flight-hour checks or annual inspections. Predictive maintenance, however, uses actual performance data to assess the health of components in real time and estimate when a failure might occur. Digital twins increase the accuracy of these models by continuously simulating operational conditions and comparing expected versus actual behavior.
Let’s say an engine’s oil pressure trends lower than normal. In a legacy setup, that might go unnoticed until a scheduled check. But with a digital twin, that deviation is immediately flagged against historical patterns, environmental conditions, and operating thresholds. Maintenance teams can intervene before a failure happens to head off downtime and safety risks.
Rolls-Royce exemplifies this with its IntelligentEngine platform. Engineers create a digital twin of an engine using real-time sensor data and satellite connectivity. The virtual model runs in tandem with the physical engine, allowing Rolls-Royce to forecast maintenance needs, simulate extreme environments, and schedule proactive repairs (Rollys-Royce).
Benefits for airlines and MRO providers
The payoff for predictive maintenance powered by digital twins is substantial, and it hits many key pain points:
- Reduced unplanned downtime: Airlines lose thousands of dollars for every grounded aircraft. Digital twins help catch problems early, allowing for preemptive action.
- Extended component life: Instead of swapping parts too early (wasting resources) or too late (risking failure), teams can base replacements on actual wear and usage.
- Smarter inventory planning: Predictive data helps MROs stock only what’s needed to cut carrying costs while improving part availability.
- Increased safety and compliance: Continuous monitoring helps ensures nothing slips through the cracks, satisfying regulators and internal audits alike.
A recent study shows that digital twin-driven predictive maintenance led to up to 30% cost reductions and 40% fewer unscheduled maintenance events across simulated airline operations (Civil Engineering Science and Technology).
Real-world applications in aviation
While the promise of digital twin technology sounds futuristic, it’s already deeply embedded in today’s aviation workflows.
Delta Airlines
Delta Air Lines is a leader in applying digital twin and AI technologies for predictive maintenance, primarily through its APEX (Advanced Predictive Engine) system (Airways Mag).
APEX collects real-time engine data throughout every flight and uses artificial intelligence to build dynamic digital replicas of each engine's current condition. These digital twins allow Delta to anticipate component wear or abnormalities long before they cause mechanical issues.
For example, if the system detects patterns—such as slight increases in vibration or temperature—it can alert technicians to replace a part within a specific window, i.e., 50 flight hours, rather than waiting for a failure. This proactive approach eliminates guesswork, reduces unnecessary replacements, and ensures maintenance is performed precisely when needed.
The results have been dramatic: from 2010 to 2018, Delta slashed maintenance-related cancellations from over 5,600 annually to just 55 (Airways Mag).
The APEX program is credited with saving the airline eight figures each year and won Aviation Week’s Innovation Award in 2024. Leveraging digital twins, Delta keeps planes in the air longer, reduces costly downtime, and delivers a more reliable experience for passengers while significantly lowering maintenance and operational costs (Airways Mag).
Boeing
In addition to using digital twins to track the performance of critical systems in a closed-loop environment, as outlined earlier, Boeing also applies digital twin technology across product development, manufacturing, and maintenance.
The manufacturer has used digital twins to model the complex folding wing-tip system on the 777X, allowing engineers to simulate structural dynamics and reduce physical prototyping (Simple Flying). Similarly, Boeing employs model-based systems engineering (MBSE) to create comprehensive digital representations of aircraft, modeling how electrical, hydraulic, and avionics systems interact (Boeing Supplier). These twins help identify potential issues early in the design phase and streamline certification.
The role of AI and machine learning
A digital twin without intelligence is just a mirror. What makes digital twins powerful is their ability to learn, adapt, and predict—functions made possible by AI and machine learning.
In aviation, these algorithms crunch vast datasets from flight logs, onboard sensors, weather feeds, and maintenance records. Over time, they learn to detect weak signals—those subtle anomalies that precede failures but would be missed by human technicians.
For example, AI can spot a 0.5% increase in vibration in a fan blade under specific weather conditions and link it to a potential fatigue issue (Information and Software Technology). The digital twin, fed by this insight, updates its simulation parameters and flags a possible defect for inspection. No human analyst would’ve caught that correlation in time.
AI also helps quantify uncertainty. Instead of binary “yes/no” predictions and decision trees, it offers probabilistic risk profiles—e.g., “There’s a 78% chance this fuel pump will degrade within 300 flight hours.” This specificity changes how airlines allocate resources, schedule checks, and manage risk.
Benefits of predictive maintenance with digital twins
Digital twin–driven predictive maintenance offers airlines and MRO significant cost savings and other efficiency benefits.
1. Reduced aircraft downtime:
Digital twins predict potential behaviors before they occur, allowing for proactive maintenance action taken during low-traffic hours or planned downtime.
2. Extended component lifespan:
Maintenance is no longer done on fixed intervals, but based on actual usage and condition. This approach helps optimize asset longevity and reduce unnecessary part replacements
3. Enhanced safety and compliance:
Digital twins support condition-based monitoring that flags anomalies before they become critical. ePlaneAI integrates MEL data with predictive analytics so that deferred items are tracked and intelligently prioritized based on risk.
4. Greener operations
When predictive models indicate what’s likely to fail and when, technicians can be better scheduled, tooling prepared in advance, and inventory stocked more efficiently. Lufthansa Industry Solutions highlights this as a path toward CO₂ reduction—since fewer last-minute fixes mean less fuel-wasting flight delays or maintenance ferry flights (Lufthansa Industry Solutions).
Integrating digital twins into existing MRO systems
The biggest hurdle isn’t understanding the power of digital twins but to get them to play nicely with legacy systems.
Many aviation organizations still rely on a patchwork of spreadsheets, standalone maintenance systems, and ERP platforms with siloed data. A digital twin has no value if it can’t access accurate, live data feeds from these sources.
That’s where companies like ePlaneAI come in. ePlaneAI connects digital twin models with ERP systems to automate maintenance triggers, part orders, compliance reporting, and technician scheduling.
If the digital twin predicts landing gear fatigue, ePlaneAI can then automatically generate the associated work order, cross-check parts availability, and ensure regulatory compliance is met for MEL deferral tracking.
The key to successful implementation lies in:
- Interoperability: APIs and connectors that pull from legacy systems and OEM portals.
- Data normalization: Structuring data so it can be interpreted correctly by AI algorithms.
- Human oversight: Ensuring engineers still review AI-driven recommendations before approval.
Future of digital twin predictive maintenance in aviation
As the industry continues grappling with tighter margins, aging fleets, and sustainability demands, predictive maintenance powered by digital twins will lead the path forward.
Emerging innovations include:
- Self-healing systems: Future aircraft systems may not just predict failures but self-correct them based on digital twin simulations in real time.
- Autonomous inspections: Paired with drones or cobots, digital twins can guide and interpret physical inspections, flagging irregularities that need human attention.
- Sustainability modeling: Optimizing flight routes and cargo loads through twin simulations can significantly reduce emissions.
- Cross-platform synchronization: Rolls-Royce’s IntelligentEngine initiative suggests a future where engines not only monitor themselves but also collaborate across fleets to share predictive learnings in real time (Rolls-Royce).
As AI models become more advanced and IoT infrastructure more robust, digital twins will become smarter, more autonomous, and more integral to managing aircraft health.
Flying smarter, sooner: Why digital twins are ready for takeoff
Digital twins are reshaping aviation today, with manufacturers and carriers like Boeing, Delta, and Lufthansa leading the way for faster, safer, more cost-efficient operations.
Ready to bring the same digital twin precision to your fleet?ePlaneAI helps aviation teams integrate predictive maintenance into their operations with powerful and streamlined integrations. From MEL deferral optimization to real-time diagnostics and smarter forecasting, we make it easier to catch issues before they ground your aircraft.
Talk to our team today and see how ePlaneAI can future-proof your maintenance strategy. Book a demo today!
Aviation Maintenance Trends That May Gain Momentum in Uncertain Circumstances
Aircraft are staying in service longer, supply chains are a powder keg, and the tech is evolving overnight. Discover the maintenance trends gaining momentum and what they mean for operators trying to stay airborne and profitable.
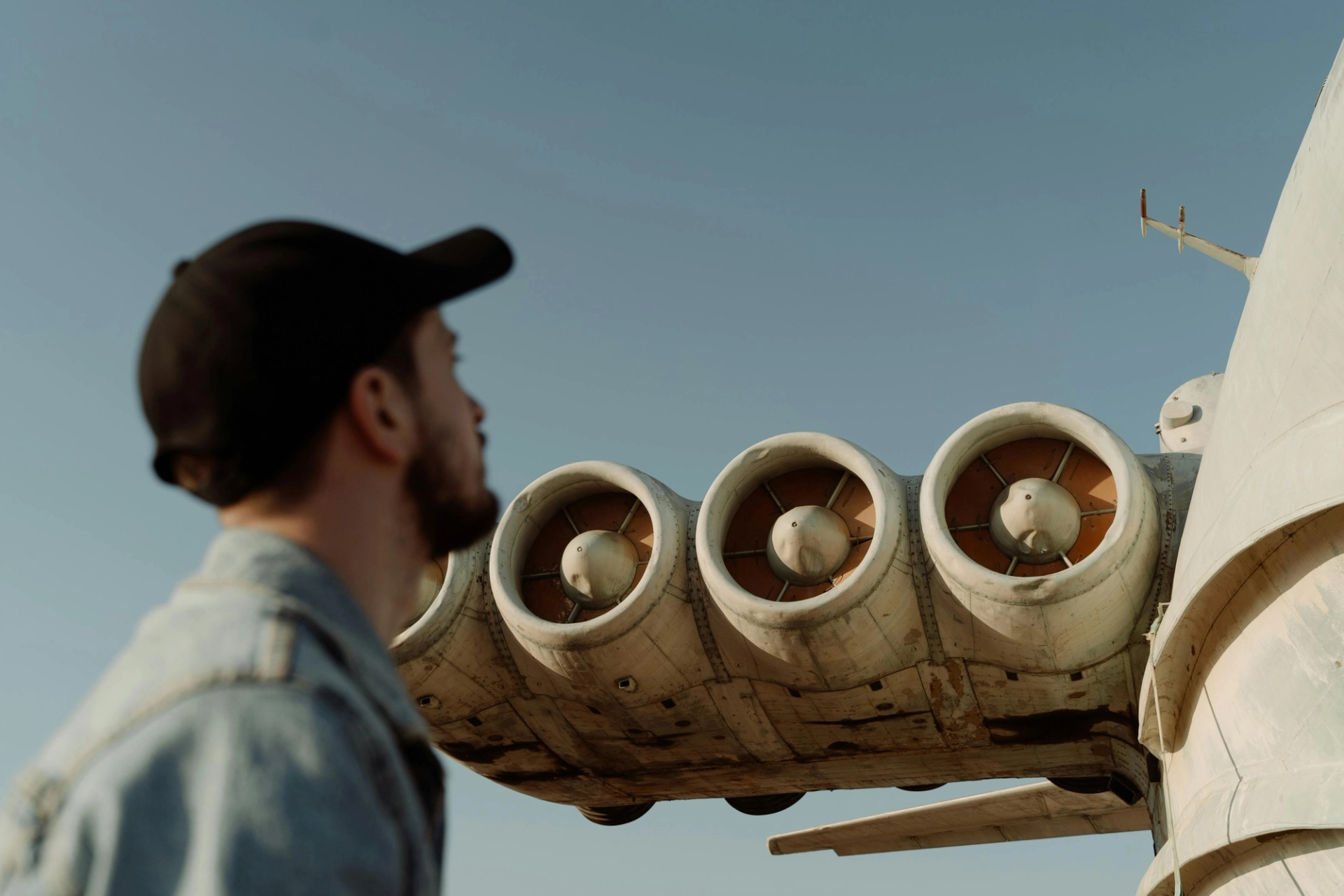
July 15, 2025
Understanding the Shelf Life of Aircraft Parts to Create Your Next Replacement Schedule
Aircraft parts don’t last forever. Learn how shelf life tracking and AI-drven planning can streamline airthworiness and compliance.
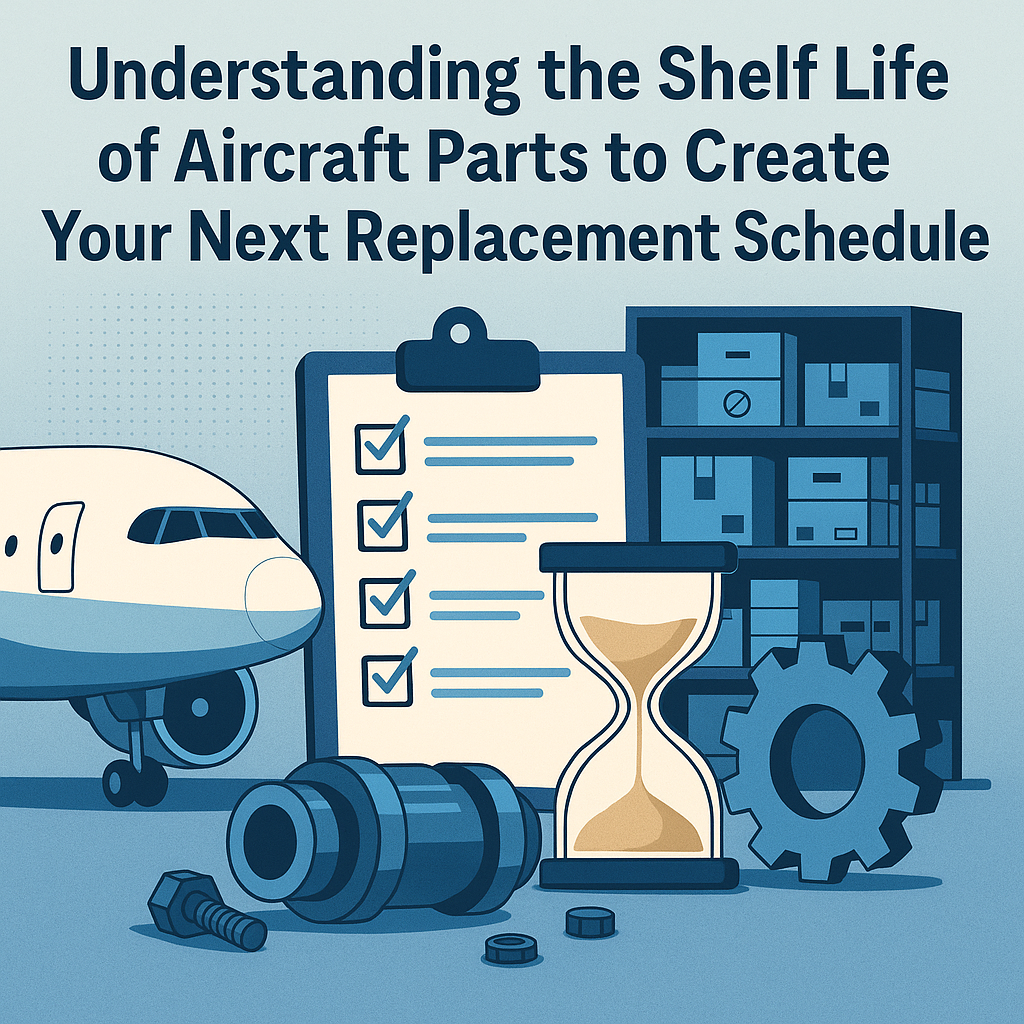
July 15, 2025
From Marketplace to Machine Learning: How We've Evolved for Aviation’s Future
Overview. We've shifted from marketplace to machine learning. Learn more about what's driven this shift and how we're driving aviation's AI-driven future into 2025 and beyond.
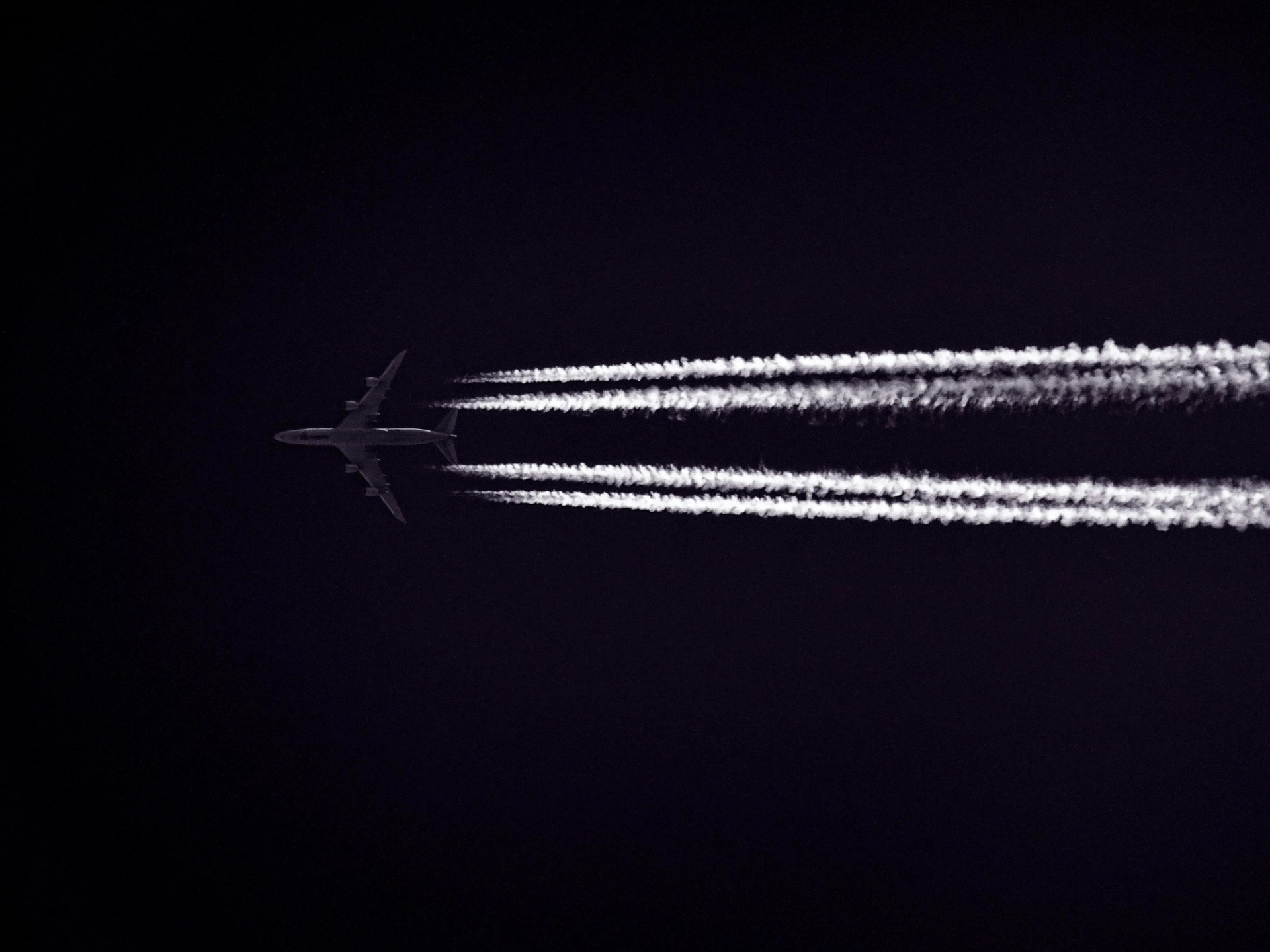
July 10, 2025
How Aviation Labor Shortages Are Affecting Spare Part Sourcing
Aviation’s labor shortage isn’t just slowing repairs—it’s gutting global parts sourcing. See how MROs and OEMs are rethinking training, tooling, and supplier strategy.
