Understanding aircraft part condition codes to ensure conformity
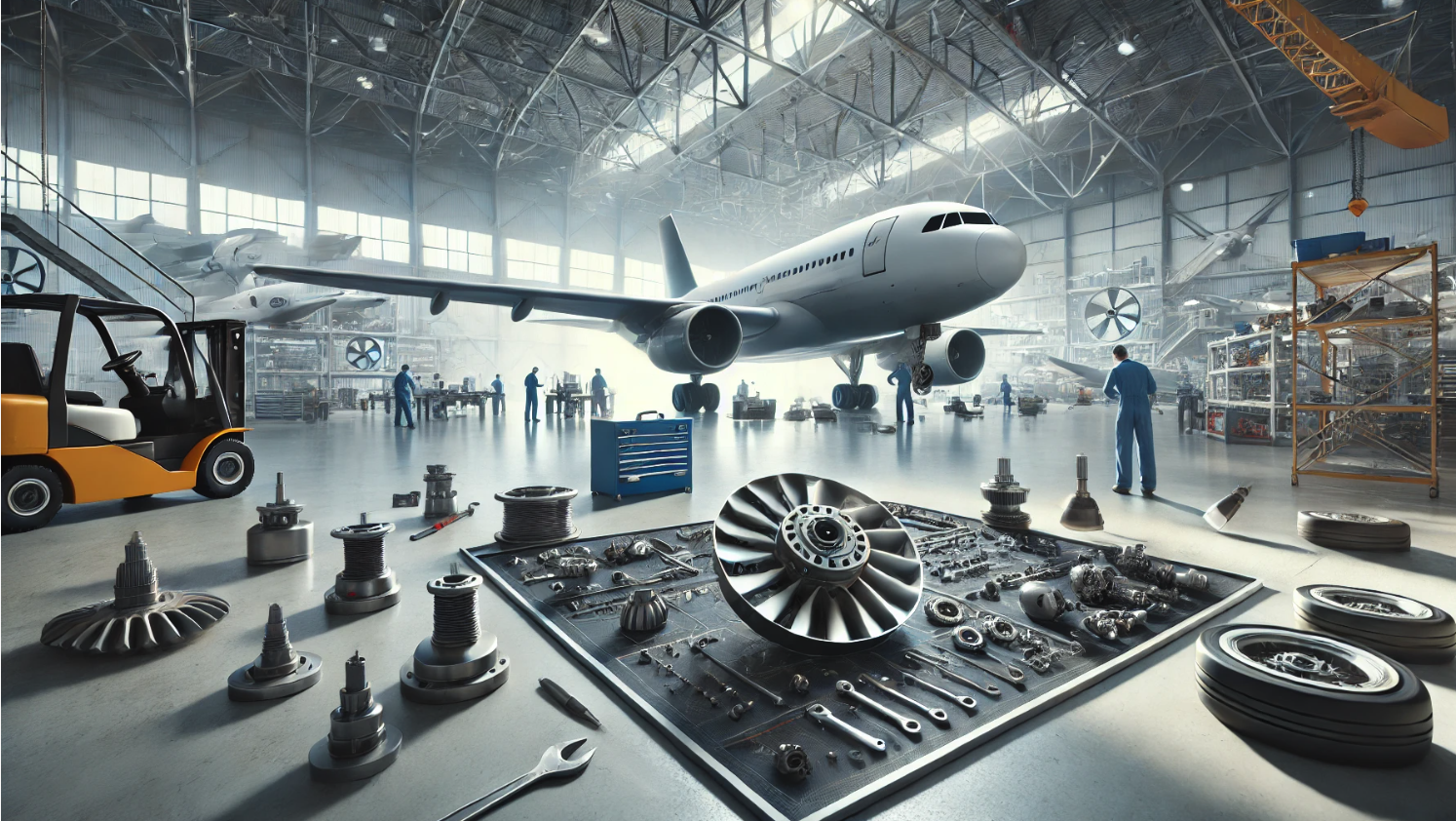
In aviation, safety is everything. Aircraft operate under strict regulations, and every component, from engines to tray tables, must meet high standards. Understanding aircraft part condition codes is essential for managing conformity, maintenance costs, and fleet airworthiness.
Condition codes classify parts based on their usability, history, and compliance with aviation regulations. Without these distinctions, operators risk installing a faulty or non-compliant component, leading to potential mechanical failures and regulatory penalties.
The part’s condition affects whether it can be safely installed and used, resold, or scrapped. This is particularly important for rotables—parts that can be repaired and returned to service.
Beyond safety and compliance, aircraft part condition codes also influence trade and logistics. Standard Industrial Classification (SIC) codes and Harmonized System (HS) codes help categorize aviation parts for global commerce for proper taxation and regulatory approval during import and export processes.
This guide will break down key aircraft part condition codes, their impact on maintenance and procurement, and how AI-powered tools like ePlaneAI can simplify compliance, tracking, and verification.
The importance of condition codes in aviation
Aircraft maintenance and procurement teams rely on condition codes to make informed decisions about parts. These classifications help determine if a component is safe to use, requires overhaul, or is beyond repair.
In 1956, the Air Transport Association of America, now known as Airlines for America (A4A), published the first numerical classification system for aircraft parts called ATA Spec 100 (A4A).
Later in 1999, the FAA developed the Joint Aircraft System/Component (JASC) Code Tables, adapting ATA Spec 100 to create a broad, standardized way to classify aircraft parts. The latest version was released in 2008 (FAA).
While not officially required by the FAA, condition codes are widely used and considered an industry best practice for tracking part history, maintaining compliance and safety. They are essential for aviation professionals who must navigate complex supply chains, where parts are sourced from multiple vendors around the globe.
With this system, companies have an objective, universal way to distinguish between airworthy and non-airworthy parts, which would be nearly impossible without a standardized guide.
Regulatory compliance
Government agencies mandate strict record-keeping for aircraft components. A missing or incorrect condition code could prevent an aircraft from passing an inspection, grounding a single aircraft, or even an entire fleet.
FAA regulations, for example, require detailed documentation proving a part’s origin, repair history, and compliance with airworthiness directives.
Cost management and efficiency
Condition codes also impact financial decisions. New parts are expensive, while overhauled parts can reduce costs and still meet safety standards. Air maintenance teams optimize budgets by purchasing certified pre-owned parts that meet regulatory requirements while costing significantly less than new components.
Risk mitigation
Incorrectly installing a part with an unknown or misleading condition code increases the risk of failure mid-flight. Every aircraft part has a lifespan, and tracking its condition so that it isn’t used past its safe operational limit is imperative.
Condition codes play a crucial role in mitigating risk. The next section will break down the most common aircraft part condition codes and their meanings.
Rotables vs. expendables: How condition codes apply
Aircraft parts are broadly classified into two categories: rotables and expendables (NSL Aerospace).
Rotables: The high-value, reusable components
Rotables are parts that can be repaired and reused multiple times throughout their lifecycle. These include landing gear, avionics modules, and auxiliary power units (APUs). Because they undergo regular overhaul (OH), repair (RP), and serviceability checks (SV), condition codes help track their airworthiness over time.
Aviation maintenance teams monitor rotable components closely, tracking time since overhaul (TSO), cycles used, and remaining service life. Armed with this data, airlines can accurately plan for repairs and replacements without disrupting operations.
Expendables: The single-use parts
Unlike rotables, expendables are used once and then discarded. These items include nuts, bolts, gaskets, filters, and lightbulbs. Since they aren’t repaired or reused, their condition codes are generally New (NE) or New Surplus (NS).
Understanding the distinction between rotables and expendables helps aviation companies make more cost-effective purchasing decisions.
In the next section, we’ll explore how SIC and HS codes help categorize aircraft parts for trade and regulatory compliance.
Industry classification: SIC and HS codes for aircraft parts
Beyond condition codes, aviation professionals must also navigate Standard Industrial Classification (SIC) codes and Harmonized System (HS) codes to ensure compliance in manufacturing, trade, and maintenance.
Both of these classification systems help categorize aircraft components for regulatory, taxation, and logistical purposes.
What are SIC codes?
The Standard Industrial Classification (SIC) system categorizes businesses based on their primary industry. Aircraft parts fall under SIC codes related to aerospace manufacturing, maintenance, and distribution.
One of the most relevant SIC codes for aviation parts is SIC Code 3728 – Aircraft Parts and Auxiliary Equipment.
This code applies to businesses that manufacture aircraft parts and auxiliary equipment not covered by other classifications. It includes everything from landing gear and propellers to de-icing systems and oxygen equipment.
Some companies under SIC 3728 also focus on research and development, either independently or through contracts (OSHA: SIC Manual).
What is the HS code for aircraft parts?
The Harmonized System (HS) code is an international standard for identifying and classifying traded goods. HS codes are critical for customs clearance, import and export documentation, and tax regulations.
The primary HS code for aircraft parts is HS Code 8803 – Parts of Goods of Heading 8801 or 8802, which covers aircraft, spacecraft, and satellites (United States International Trade Commission USITC).
HS codes provide a structured way to determine tariffs, prevent counterfeit parts from entering supply chains, and maintain compliance with international trade agreements (United States International Trade Administration ITA).
Understanding and applying the correct SIC and HS codes helps businesses avoid customs delays, penalties, and regulatory non-compliance. In the next section, we’ll explore best practices for managing compliance when procuring and installing aircraft components.
Ensuring compliance and best practices
Aircraft maintenance and procurement teams must follow strict quality control processes to help ensure that every part meets regulatory requirements before installation.
Below are best practices for compliance and risk reduction:
Verify condition codes and documentation
- Always check an aircraft part’s condition code before purchase or installation.
- Verify parts come with proper traceability documents like the FAA Form 8130-3 or EASA Form 1, which confirm airworthiness and manufacturing design specifications.
- Avoid parts labeled "As Removed (AR)" unless you have the resources to conduct supplier due diligence.
- Work only with certified suppliers that comply with FAA, EASA, and ICAO (International Civil Aviation Organization) regulations.
- If purchasing from secondary markets, verify the supplier’s track record to avoid counterfeit or unapproved parts.
Implement digital tracking systems
- Use AI-driven tools like ePlaneAI to automate part verification and track condition codes.
- Integrate blockchain-based tracking for enhanced security and transparency in the supply chain and store compliance documents digitally.
Maintain a robust recordkeeping system
- Log every part’s installation date, condition updates, and repair history to stay ahead of audits and inspections.
- Check that all maintenance actions align with regulatory airworthiness directives (ADs).
In following these best practices, aviation companies can minimize compliance risks, prevent unplanned downtime, and maintain safe air fleets.
Next, we’ll explore how AI and emerging technologies are transforming aircraft parts management.
The future of aircraft parts management
As aviation technology advances, AI, machine learning, and blockchain are transforming how aircraft parts are tracked, verified, and managed. These innovations bring new levels of efficiency, reduce errors, and streamline regulatory compliance.
AI-powered predictive maintenance
Traditionally, aircraft maintenance follows either fixed schedules or reactive repairs (when a part fails). AI offers a better approach. Enabling predictive maintenance, which uses real-time data, AI can accurately anticipate when a part will fail, need replacement, or require an overhaul.
- Airlines and maintenance teams can use AI-powered tools like ePlaneAI to analyze sensor data, detect early signs of failure, and optimize part replacements before an issue causes flight delays.
- AI also helps with automated condition classification, keeping parts correctly labeled and compliant with aviation regulations.
Blockchain for supply chain transparency
One of the biggest challenges in aircraft parts management is verifying part authenticity and tracking its usage and movement history. Counterfeit parts pose serious safety risks, but blockchain technology helps prevent fraud by creating a tamper-proof digital record of each part's lifecycle.
- Blockchain technology can help ensure that every aircraft component has a verifiable and immutable history, from manufacturing to installation.
- It also enhances trade compliance by linking parts directly to SIC and HS codes, reducing import and export discrepancies.
Automation and digital twin technology
- Digital twins create virtual replicas of aircraft components, allowing for real-time condition monitoring.
- Automated inventory management reduces manual errors and optimizes part availability.
These innovations are setting a new standard for speed, safety, and cost savings in aviation.
Common air part condition codes for new and used parts
Aircraft parts are classified by condition codes that indicate their usability, history, and compliance.
Below are the most common condition codes used in the aviation industry:
New and like-new parts
- FN – Factory New: A brand-new part from the Original Equipment Manufacturer (OEM), produced within the last two years. It comes with full certification, traceability, and a manufacturer’s warranty.
- NE – New: A new part that has never been used, with no operating time or cycles. It retains OEM certification and all necessary trace information.
- NS – New Surplus: A new part that meets manufacturer standards but may have changed hands multiple times. It has no prior usage but may lack full original documentation from the OEM.
Serviceable and overhauled parts
- SV – Serviceable: A used part that has been inspected, tested, and certified as airworthy for installation.
- OH – Overhauled: A part that has been fully disassembled, inspected, repaired as necessary, reassembled, and restored to like-new condition following the manufacturer’s Component Maintenance Manual (CMM).
Used and repairable parts
- AR – As Removed: A part taken from an aircraft in its existing condition, with no testing or inspection. It may still be functional but requires evaluation before reuse.
- IN – Inspected: A removed part that has undergone a general inspection and been verified as defect-free but has not received any repairs or modifications.
- RP – Repaired: A part that was previously faulty or worn and has been restored to airworthy condition through an approved repair process. Repair details are documented in a teardown report.
- RB – Rebuilt: A used part that has been fully disassembled, inspected, repaired, reassembled, tested, and approved to meet the same tolerances and limits as a new part. Unlike an overhauled part, a rebuilt part may incorporate both new and used components.
Modified and tested parts
- MO – Modified: A part that has been altered from its original configuration, either through structural changes, software upgrades, or other engineering modifications. These changes must meet approved regulatory guidelines.
- TS – Tested: A component that has undergone an approved inspection and test procedure to verify its functionality. This can include function testing, operational cycle testing, or a bench check.
- FT – Function Tested: A part that has been tested for operational performance but has not undergone repairs or modifications. This is common for components that require periodic testing, such as flutter dampers and avionics modules.
Non-serviceable and end-of-life parts
- RJ – Rejected: A part deemed unfit for use due to defects, excessive wear, or inability to meet airworthiness standards.
- BER – Beyond Economical Repair: A part that is technically repairable but the cost of repair exceeds its value or replacement cost. This often applies to outdated components with unavailable replacement parts.
Mastering aircraft part condition codes
Aircraft part condition codes are more than just industry jargon; they provide a uniform language for discussing and documenting aviation safety, regulatory compliance, and cost efficiency. Whether managing a fleet, sourcing spare parts, or performing maintenance, understanding these codes helps prevent costly errors and operational disruptions.
As aviation continues to evolve, integrating digital solutions like ePlaneAI into aircraft parts management will be essential.
Looking for a smarter way to manage aircraft parts? Explore how ePlaneAI can streamline your procurement, verification, and compliance processes—so you always have the right part, in the right condition, at the right time.