Understanding the True Cost of Spare Parts in Aviation Procurement
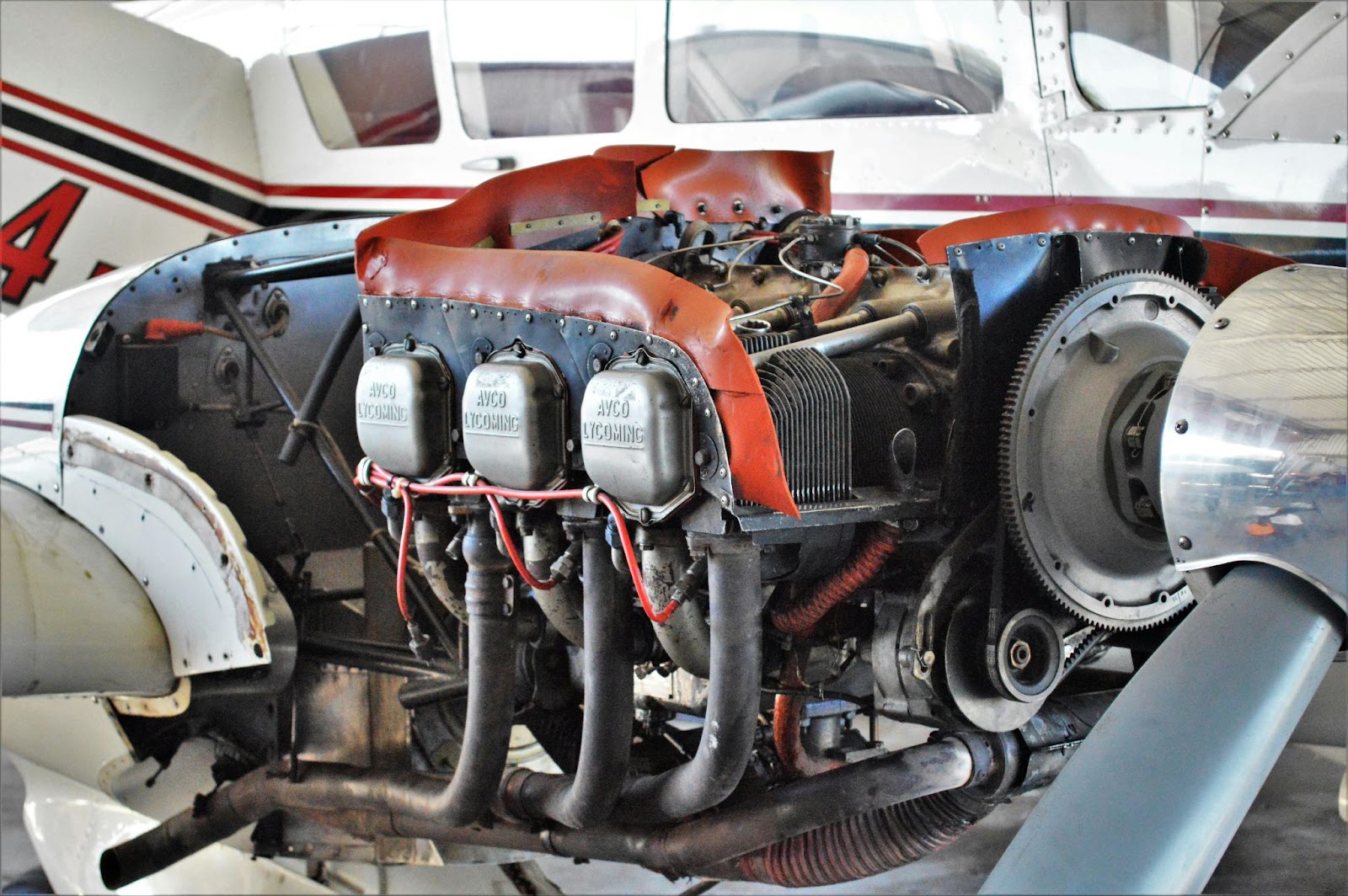
Managing the cost of spare parts in aviation procurement is far more complex than simply comparing price tags. Airlines, maintenance providers, and leasing companies must navigate a web of hidden expenses, logistical hurdles, and regulatory requirements that can significantly inflate procurement costs. Understanding these factors is critical for maintaining fleet efficiency and financial stability.
Spare parts procurement, and often overprocurement, directly impacts an airline’s bottom line. Delays in sourcing essential components can lead to aircraft on ground (AOG) incidents, resulting in significant revenue loss.
Similarly, maintaining excess inventory leads to high storage, inventory management, and depreciation costs. With airlines spending billions annually on spare parts, optimizing procurement strategies can yield substantial cost savings.
This article breaks down the true cost of spare parts in aviation procurement, highlighting hidden costs, regulatory challenges, logistics expenses, and opportunities for digital transformation. Understanding these factors, aviation companies can implement smarter procurement strategies.
Breaking down the true cost of spare parts
The cost of spare parts in aviation extends far beyond the initial acquisition price. Airlines must consider hidden expenses such as shipping fees, customs duties, warehousing costs, and the impact of delays on fleet operations. These costs add up quickly, making strategic procurement essential.
One of the biggest cost drivers is aircraft-on-ground (AOG) events, which occur when an aircraft is grounded due to unavailable parts. AOG incidents and other unplanned delays cost airlines $30 billion annually, primarily due to lost revenue, passenger compensation, and last-minute procurement expenses (AAA Air Support).
Additionally, spare parts pricing fluctuates based on market demand, lead times, and supplier availability. Airlines often pay a premium for expedited shipping, especially when parts must be flown in internationally.
Another hidden cost is part obsolescence. Aircraft components have limited production lifespans, and once a manufacturer discontinues a part, airlines may have to pay steep premiums for last-available inventory or invest in costly retrofitting solutions.
A 2024 McKinsey & Company study reveals companies could reduce inventory costs by 35% through a more proactive, data-driven approach (McKinsey & Company: Addressing Continued Turbulence: The Commercial-Aerospace Supply Chain).
Understanding these hidden expenses allows airlines to develop more cost-efficient acquisition models, such as strategic supplier agreements, predictive maintenance planning, smarter inventory rotation, and alternative sourcing methods to minimize financial impact.
Inventory management and storage costs
Effective spare parts management is an expensive balancing act. Maintaining too much inventory ties up capital and increases storage expenses, while too little can lead to costly delays.
Aerospace inventory management is notoriously inefficient. Airlines have over $10 billion tied up in annual, excess inventory costs (Forbes), representing about 21% of total inventory value (Skylink International).
Aviation companies must contend with the upfront purchase costs, and then additional fees for storage, maintenance, insurance, and depreciation.
Storage costs come packed with many hidden costs that go beyond warehouse rent, including climate–controlled storage units, security, labor costs, and inventory management fees. As spare parts can degrade over time, with improper storage conditions speeding up deterioration leading to increased financial losses.
To mitigate these costs, many aviation companies implement just-in-time (JIT) inventory strategies, which aims to reduce excess stock and ensure that critical components are always available when needed. However, this approach comes with risks. Shortages can lead to grounded flights and other delays.
A more balanced approach is predictive inventory management, which leverages AI-driven analytics to forecast demand trends and part failure rates. These models take into account both historical data and external factors for greater accuracy.
According to the Department of Energy, this approach may reduce maintenance costs by up to 30% (NASA Technical Reports Server). With these efficiency wins, companies are pivoting to predictive inventory management; its global market is expected to grow at a CAGR of 17% by 2028 (Science Direct: Procedia Manufacturing).
Logistics and transportation expenses
The logistics of aviation spare parts procurement is a significant cost driver, especially when dealing with emergency shipments and global supply chain disruptions. Airlines often need rapid part deliveries to minimize AOG time.
Shipping fees aren’t widely published, but fleets can expect to pay up to 200% more for expedited shipping over standard freight options.
Beyond expedited shipping, other key logistics costs include:
- Customs and import duties: International shipping involves regulatory fees, tariffs, and compliance costs, which can add 15% or more to procurement costs. If anti-dumping duties or other special tariffs are applied, they could go even higher.
- Freight forwarding fees: Specialized handling is required for fragile, oversized, or hazardous components, increasing transport costs.
Global supply chain disruptions further complicate logistics. Delays in customs clearance, transportation strikes, or supplier shortages can cause shipment delays, forcing aviation companies to resort to costlier procurement options to avoid flight cancellations.
The global connectivity, however, also enables companies to tap into a much larger network of suppliers for more competitive pricing and parts availability, reducing reliance on emergency shipments.
Regulatory compliance and certification costs
Aviation spare parts must meet strict regulatory requirements set by the FAA, EASA, and other governing bodies, ensuring safety and airworthiness.
However, compliance comes with additional costs, including certification fees, administrative overhead, and the risk of regulatory delays.
Every spare part must have proper documentation, such as an FAA 8130-3 or EASA Form 1, proving it meets safety standards.
Certification delays can add weeks to procurement timelines, disrupt maintenance schedules, drive substantial revenue losses, ground aircraft, and incur hefty fines.
In one noted example, the FAA proposed $633,009 in penalties against Space Exploration Technologies Corp (SpaceX) for failing certification requirements in two launches in 2023 (FAA Newsroom).
Fines can far exceed that figure. FAA fines for non-certification can reach up to $1,200,000 per infraction for businesses and non-individual entities (FAA Legal Enforcement Actions).
Key compliance costs include:
- Regulatory audits and inspections for spare parts compliance, which can cost airlines millions of dollars annually.
- Documentation errors, which lead to additional administrative costs and delays.
- Counterfeit parts prevention, as failing to verify part authenticity can result in safety risks and legal liability.
To minimize these costs, airlines are investing in blockchain technology and other digital compliance tracking systems, which automate certification management and reduce paperwork errors.
Using AI solutions like ePlaneAI’s Document AI can automate document management and demanding audit preparation tasks. The challenge lies in records scattered procurement and MRO records across different departments, software systems, and data-capture formats, but with automation, companies slash audit preparation time by up to 50%.
Supplier relationships and procurement strategies
Aviation companies must navigate complex supplier relationships to secure cost-effective, high-quality spare parts. Choosing the right suppliers impacts pricing, lead times, and part availability, making procurement strategies a critical factor in cost management.
Vendor pricing models can vary significantly, with some suppliers offering volume-based discounts, while others charge premium prices for on-demand availability.
Strategic partnerships with reliable suppliers can cut procurement costs and reduce reliance on last-minute sourcing.
Procurement strategies that reduce costs include:
- Long-term contracts: Establishing multi-year agreements with suppliers locks in pricing and guarantees priority access to critical parts.
- Multi-source procurement: Relying on multiple vendors prevents shortages and reduces price volatility.
- AI-driven sourcing platforms: Automated procurement software streamlines supplier negotiations and ensures cost efficiency.
Another cost-saving method is pooling resources through airline alliances, where carriers share spare part inventories, reducing the need for each airline to stockpile its own costly inventory.
By implementing data-driven procurement strategies, airlines can optimize supplier relationships, reduce spare parts costs, and ensure continuous access to essential components without inflating operational expenses.
The impact of digital transformation on spare parts costs
Digital transformation is reshaping spare parts procurement, allowing airlines to cut costs by leveraging AI, automation, and blockchain technology.
Traditionally, procurement has been a manual and reactive process, leading to delays, human errors, and inflated costs. However, digital advancements now enable data-driven decision-making and predictive procurement strategies.
Key digital innovations reducing spare parts costs:
- AI-powered forecasting: Predictive analytics identify when and where spare parts will be needed, reducing emergency orders and shipping expenses.
- Blockchain for supply chain transparency: Ensures authenticity of spare parts, reducing fraud and eliminating counterfeit components.
- Automated procurement systems: Airlines using AI-based procurement could lower business costs by up to 40% through digital spend cubes and AI automation (McKinsey & Company: Overcoming Challenges in Aerospace Procurement).
Hidden costs and financial risks in spare parts procurement
Beyond visible expenses, airlines face hidden costs and financial risks in spare parts procurement. These include currency fluctuations, supply chain instability, and hidden fees associated with purchasing, warehousing, and shipping.
Major hidden costs in aviation spare parts procurement:
- Counterfeit parts risks: The global aviation industry loses millions annually due to fraudulent components. Using non-certified parts can lead to catastrophic failures and regulatory penalties of up to $1.2 million (FAA Legal Enforcement Actions).
- Currency volatility: Exchange rate fluctuations impact imported parts costs, especially for airlines purchasing from international suppliers.
- Insurance gaps and warranty limitations: Airlines that fail to negotiate comprehensive warranty terms risk paying out-of-pocket for defective parts, driving up maintenance costs.
- Excessive contract penalties: Some supplier agreements include high fees for early contract termination or emergency order surcharges.
To mitigate these financial risks, airlines are adopting cost modeling techniques and diversifying supplier networks. Aviation companies adopting this varied approach can better control expenses and minimize financial exposure in the spare parts market.
Smarter strategies for managing spare parts costs
Controlling spare parts costs is about more than just finding the lowest price. Airlines need better forecasting, stronger supplier relationships, and more efficient procurement processes to avoid waste and unnecessary expenses. AI and automation make it easier to predict demand, streamline sourcing, and reduce financial risks.
ePlane AI helps airlines cut costs, improve efficiency, and stay ahead of supply chain disruptions. Our AI-powered procurement tools simplify sourcing, reduce delays, and optimize inventory management. Talk to us today to see how ePlane AI can transform your procurement strategy.