Leveraging Technology to Optimize Aircraft Spare Parts Inventory Management
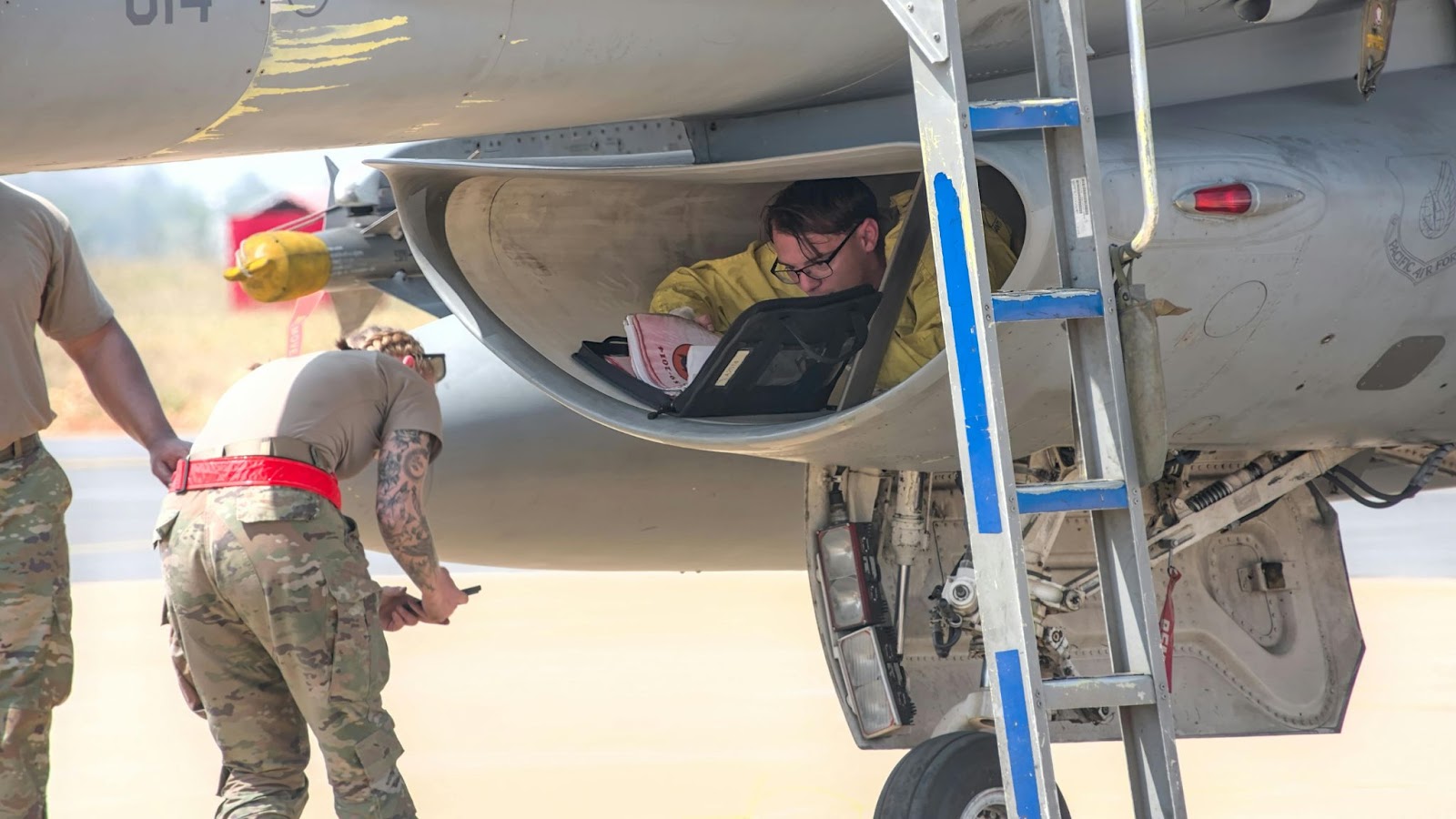
In the aviation industry, a single missing part can bring company-wide operations to a halt. Any unexpected event—especially when it relates to mission-critical components—can ground an aircraft, delay flights, and result in costly financial repercussions.
Expert spart parts inventory management is an industry imperative. Today’s aviation leaders are turning to technology to gain tighter control, streamline procurement workflows, reduce aircraft downtime, and manage compliance.
With predictive maintenance systems, real-time tracking solutions, and intelligent procurement platforms, managing inventory has evolved into a data-driven discipline that touches every part of the supply chain. This article explores the technologies, best practices, and strategic considerations now involved in managing aviation spare parts.
The unique challenges of managing aircraft spare parts inventory
Complex parts with high stakes
Aircraft spare parts fall into two primary categories: rotables and expendables.
- Rotables include high-value components like avionics, landing gear, and flight control surfaces, parts designed to be repaired and reused.
- Expendables are lower-cost, single-use parts like seals, filters, or screws. Both types are essential to operations and demand precise oversight.
Every part has a lifecycle to manage and documentation requirements to meet. Some parts are mission-critical; if they fail, the aircraft can’t fly. Others can be deferred and replaced later. But even those lower-priority parts need to be managed carefully to avoid ballooning costs, waste, or compliance issues. Adding to the complexity, aviation supply chains involve OEMs, MRO providers, airlines, and logistics firms that must work together — although not always in sync. Inventory strategies rely on outside partners for part availability, lead times, maintenance cycles, and compliance documentation.
Recent supply chain constraints and a historic aircraft production backlog—now exceeding 16,000 orders for narrow- and wide-body aircraft—are forcing airlines to keep aging aircraft in service longer, which is increasing pressure on spare parts availability and maintenance planning (McKinsey & Company: What does the future hold for commercial-aviation maintenance?)
The cost of mismanagement
Letting inventory numbers dip below optimal thresholds, even slightly, can lead to cascading problems. When a critical part isn’t available and an aircraft cannot fly, an AOG (aircraft on ground) event occurs. The costs to resume operations can quickly skyrocket, including emergency sourcing fees, rapid transport costs, labor overtime, and lost revenue from canceled or delayed flights.
These disruptions can also pressure the airline’s balance sheets, especially if they happen repeatedly or affect long-haul, high-revenue flights. Beyond financials, operational failures damage customer trust and expose carriers to regulatory scrutiny.
Core technologies driving inventory optimization
Predictive maintenance and condition-based monitoring
Traditionally, aircraft fleets have relied on scheduled maintenance or reactive repairs when parts failed. But thanks to predictive maintenance, operators can now spot signs of failure well before they become emergencies.
Systems like Prognos, developed by AFI KLM E&M, use aircraft health monitoring and historical data to flag potential part failures in advance. This minimizes downtime and gives teams time to prepare the necessary inventory (Aviation Week).
At the same time, condition-based monitoring (CBM) uses sensors to gather data like temperature, vibration, or fluid levels. These insights can indicate whether a component is still operating within acceptable parameters. When deviations occur, maintenance can be scheduled proactively rather than waiting for breakdowns (The Yale Wave). A CBM approach can also prevent unnecessary component replacements, as many older parts may still be fit for use.
These tools empower airlines to stock only what’s likely to be needed, rather than holding excessive “just in case” inventory.
Inventory management software
Modern inventory management software brings structure, speed, and visibility to aviation parts tracking. Modern platforms can centralize inventory records, automate procurement, and facilitate regulatory compliance across the entire supply chain.
Acctivate, for example, supports real-time monitoring of parts, tracking stock movement, and flagging low inventory levels. It also enables barcode-based identification, making it easy to locate parts quickly and eliminate manual tracking errors.
These inventory systems also streamline procurement by automating purchase order creation, monitoring vendor performance, and integrating demand forecasts. This level of automation not only improves accuracy but also minimizes costly emergency orders and reduces excess stock that might never be used.
Forecasting, analytics, and data-led decisions
Data is the currency of effective inventory management. Forecasting tools help organizations anticipate demand for parts based on flight usage, historical consumption patterns, maintenance schedules, and external factors like seasonal weather.
Florent Michel of APOC (Aircraft Part-Out Company) notes that successful inventory programs are built around fast access to relevant data: past transactions, market demand, and technical specifications. This allows decision-makers to analyze what’s on the shelf, understand what’s moving, and identify which parts are underutilized or obsolete. Without that visibility, it’s easy to miss opportunities or stock up on the wrong things (Aviation Business News).
This is especially important now, as airlines are extending aircraft service lives to bridge new production delays. These older fleets demand more frequent and costlier maintenance, making accurate forecasting and data-informed procurement more critical than ever (McKinsey & Company: What does the future hold for commercial-aviation maintenance?).
Forecasting also supports budgeting and long-term planning. Rather than reacting to shortages, companies can align their stock levels to more accurately forecasted needs and avoid tying up capital in overstock.
Best practices for smarter inventory control
Adopt just-in-time and ABC analysis
The just-in-time (JIT) model allows aviation organizations to reduce overhead by stocking only what they need when it’s needed. While this approach is risky without solid forecasting and dependable suppliers, it reduces carrying costs and minimizes waste. Inventory management experts recommends pairing JIT with ABC analysis, a technique that groups inventory based on importance and value.
- “A” items are high-value or mission-critical.
- “B” items are still important but less urgent.
- “C” items are low-cost and infrequently used.
This approach helps allocate resources where they’re most needed. For example, parts in the “A” category may require tighter stocking thresholds, more frequent audits, and stronger supplier contracts. Meanwhile, “C” parts can be ordered reactively or in bulk with minimal risk.
Optimize warehouse layout and auditing
A poorly organized warehouse can delay aircraft maintenance just as much as a missing part. If staff can’t locate a component quickly, it slows down repairs, increases labor costs, and raises the likelihood of errors. Inventory experts recommend organizing warehouses for easy access to high-turnover or mission-critical parts. Clear signage, logical groupings, and space-efficient shelving can speed up order picking and reduce handling mistakes.
Regular inventory audits are equally important. Whether it’s full physical counts or cycle counting, audits catch discrepancies between system records and actual stock. Without them, errors accumulate, leading to shortages or overstock. Auditing also supports compliance and helps identify slow-moving parts that may be candidates for salvage yards, liquidation, or reallocation.
Manage obsolescence and part lifecycle
Aircraft parts don’t last forever, and with technology evolving rapidly, obsolescence is becoming an increasingly frequent issue. Keeping outdated parts in stock takes up space, ties up capital, and creates compliance risks. Inventory management experts emphasize the need for lifecycle management, including tracking expiry dates and flagging obsolete inventory for disposal or replacement. Connected software systems allow all teams to track parts, monitoring goods by serial or lot number. This oversight makes it easier to monitor each item’s age, condition, and usage history. Smart lifecycle tracking also supports better forecasting. Here, teams can identify which parts are nearing retirement and can plan replacements in advance.
From 2024 to 2026, aircraft are being retired 24% less often than before the pandemic, meaning more aging planes will stay in service longer, with many with parts nearing the end of their usable life. Lifecycle planning tools need to reflect this shift (McKinsey & Company: What does the future hold for commercial-aviation maintenance?).
Strengthen supplier relationships
Reliable suppliers are key to any efficient inventory management system. When your supplier delivers late or ships the wrong part, every downstream process suffers, from aircraft uptime to passenger satisfaction. Strong supplier relationship management (SRM) is critical.
Robust IT systems can notify inventory managers when it’s time to reorder and provide real-time visibility into supplier performance for rates, quality, on-time delivery, compliance documentation, and storage conditions. These insights, stretching far beyond price tags and shelf quantity, allow for much smarter buying decisions and more business leverage during negotiations.
Some companies are heavily invested in using data and market trends to assess supplier performance, while others may choose to outsource the procurement process entirely to third-party partners who maintain ready-to-ship inventory. This model reduces the internal burden and offers access to a larger, more reliable store of spare parts. However, this added convenience means less control and higher costs.
Outsourcing vs. in-house inventory: What works best?
When it comes to managing aircraft spare parts, airlines and MRO providers must choose between building an internal inventory system or outsourcing the workload to third-party suppliers. Each option has its advantages and trade-offs.
In-house inventory gives carriers more direct access to parts, allowing for quicker repairs and tighter control over compliance. This can be especially beneficial for rotables or frequently used components that could delay flights if not immediately unavailable. However, maintaining in-house stock requires significant investment, warehouse space, and experienced staff.
Outsourcing to third-party providers, however, reduces these operational burdens. These supplier companies stock and ship spare parts on demand, often across multiple clients. While this added external layer can introduce cost premiums and create business dependency, it allows airlines to focus on flying and other related operations instead of stockpiling spare parts.
Increasingly, many inventory experts advocate a hybrid model that combines operational expertise with predictive tools to optimize dispatch reliability and minimize unnecessary stock. The right choice depends on the operator’s fleet size, cash flow, and maintenance strategy.
Sustainability and cost savings through smarter inventory
Beyond managing budgets and optimal flight time, efficient spare parts management also has a sustainability component.
Overstocked parts often expire before they’re used, resulting in waste and excess carbon emissions from unnecessary production and transport. Leaner inventory models, using forecasting tools, real-time data, and just-in-time procurement, can significantly reduce such harmful impacts.
Software with advanced AI capabilities can also aid in minimizing waste. Businesses with smarter demand planning can avoid excessive deliveries and obsolete part buildup. ePlaneAI, as one example, is a powerful layer that integrates with existing ERP and inventory management systems for faster, smarter inventory procurement and other operational workflows.
When airlines manage their inventory based on real-time data, examining actual usage patterns, not blanket estimates, they can avoid unnecessary orders, lower warehouse emissions, and reduce the volume of discarded components.
More sustainable inventory management is good news for the planet (and public messaging), and it also cuts carrying costs, improves warehouse efficiency, and aligns with broader ESG goals across the aviation sector.
Bottom line: Smart tech is essential for spare parts success
Aircraft spare parts inventory management has always been a balancing act, but with today’s technology, it can be done more accurately and efficiently than ever before. It doesn’t have to be a (part) guessing game. Digital tools like predictive maintenance platforms, real-time tracking software, and automated procurement systems allow operators to be proactive, not reactive.
Aviation companies and MROs investing in smart systems and strategic partnerships can keep planes flying, avoid costly AOG events, and maintain safety compliance—without overspending or overstocking. In an industry where margins are tight and expectations are high (borderline fantastical), advanced technology can shoulder much of the operational burden.
At present, AI is redefining every part of the industry. It’s not just AI copilots and faster engines; technology is reshaping how companies buy, store, and reorder spare parts. As the global fleet continues to grow and shift toward next-generation aircraft, airlines and MROs must also prepare for evolving maintenance demands that balance today’s aging aircraft with tomorrow’s composite-heavy, data-rich fleets.
Ready to modernize your parts inventory strategy?
ePlaneAI integrates seamlessly with your existing ERP and inventory management systems to accurately forecast demand, reduce waste, and keep your fleet in the air. Learn how ePlaneAI can power your operations.