How Real-Time Inventory Management Prevents Stockouts and Reduces Holding Costs
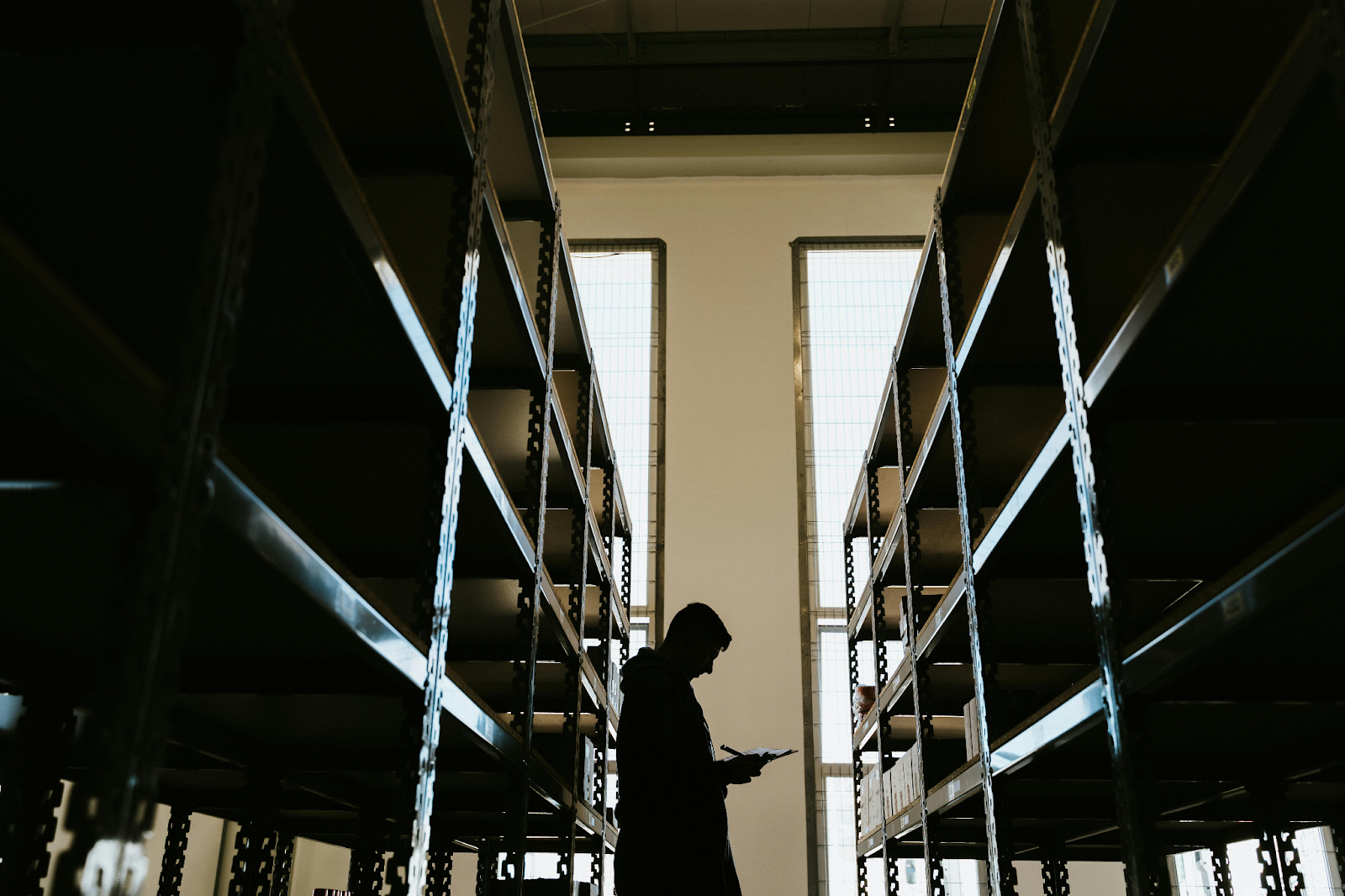
Managing inventory is a delicate balancing act. You don't want a missing part to be the reason, again, that a flight gets grounded. Certainly not on your watch! Yet, on the other hand, excess inventory can cost a bundle. Overstocked goods tie up capital, increase storage and MRO costs, and are at risk for obsolescence. For aviation companies, the problem is compounded further when many aircraft parts and avionics have a run life of up to five years while hulls in contrast are built to last for decades.
Managing aviation inventory is an intricate game of high-usage components with precise and widely varying usage requirements. Real-time inventory tracking and automated alerts can manage these complexities and bring radical efficiency to inventory management. This article looks at the benefits of real-time inventory management with AI and stock alerts, and automated inventory management solutions like ePlaneAI.
How stockouts and excess inventory disrupt aviation operations
The burden of excess inventory
Excess inventory presents a different but equally critical problem. Aviation companies frequently stock high-value parts as a buffer against shortages, but this strategy comes at a cost. Holding inventory for extended periods ties up working capital and increases storage fees.
The exact carrying costs of this surplus inventory are hard to calculate. Many online articles cite a figure of 30%, claiming 30% of a company's total inventory value annually. There is, however, no published original study or source to substantiate that figure.
Skylink International, a global provider of aviation logistics and supply chain solutions, estimates that stale inventory costs $10 billion a year, or 21% of total inventory value. Because of inventory management challenges, Skylink says a huge fraction of spare parts and other MRO inventory are never used.
Real-time inventory tracking in action
Inventory management today isn’t what it used to be. There was a time when teams could sit down, do a stock check, and feel confident the numbers would hold steady until the next order—but those days are long gone. Now, the moment you finish counting inventory, it’s already outdated. The speed at which the industry moves makes it nearly impossible to keep up using traditional methods. And let’s be honest, these manual processes are a beast: It’s no wonder many teams are reluctant to do stock checks as frequently as they should.
But the reality is that tracking inventory once a month, once a week, or even once a day just doesn’t cut it anymore. Real-time inventory tracking is the only way to keep up with ever-changing stock levels and ensure your operations stay ahead of the curve.
A real-time approach gives aviation companies an up-to-the-minute view of stock levels, enabling teams to make informed purchasing and MRO maintenance decisions. Automated alerts flag low stock or parts nearing end-of-life, ensuring that grounded flights are avoided and excess inventory doesn’t linger until it’s worthless or devalued. With real-time tracking, you’re not just keeping up—you’re staying ahead.
Automated alerts
A proactive alert system issues notifications when inventory falls below predefined thresholds. This ensures timely reordering which is especially critical for components like turbine blades and landing gear.
When your inventory tracking system is synced to your ERP or order management system (OMS), and inventory levels reach a pre-set level, this can trigger an automatic reorder or a new RFQ. Boom - self-maintaining PAR levels or something like that.
Enhanced visibility
Real-time inventory systems eliminate guesswork by providing immediate visibility into inventory levels across all storage locations. For global aviation companies, this provides a centralized view of where all parts are so they can be distributed most efficiently to minimize waste and meet demand where needed most.
Proactive demand planning
Real-time tracking goes hand in hand with predictive analytics for proactive demand planning based on historical data and usage trends. When seasonal travel spikes, severe weather, or unexpected maintenance needs can strain inventory. Real-time data allows aviation companies to preemptively stock essential parts anticipating that seasonal spike, so as to minimize the likelihood of stockouts and not get caught off guard.
Balancing inventory with smarter alerts
Optimized stock levels
Real-time inventory systems continuously analyze usage rates to ensure the right parts are ordered, stocked, redistributed and stored in alignment with actual demand. ePlaneAI's predictive tool, for example, adjusts inventory dynamically and sends alerts when parts are running low or flags under-used parts.
Flagging slow-moving parts
Real-time systems can identify slow-moving parts nearing obsolescence, allowing teams to take corrective action. Options include redistributing parts to locations with higher demand, bundling slow-moving parts with high-priority ones, or liquidating them through a marketplace (such as ePlane.com—yes, we have an aviation parts marketplace too, which shows just how serious we are about the aviation supply chain) to recover costs.
Reducing waste
Many aviation components have expiration dates or other regulatory constraints that can shorten shelf life. Real-time monitoring and inventory alerts ensure that these parts are used before they expire, reducing waste and minimizing compliance risks. AI-driven tools like ePlaneAI can prioritize the allocation of time-sensitive inventory.
Setting the right PAR levels with predictive analytics
Before effective inventory management can occur, it’s crucial to establish accurate PAR (Periodic Automatic Replenishment) levels—knowing the "just right" number of parts to have on hand at any given time. Real-time inventory tracking is only half the equation; predictive analytics plays a vital role in determining these optimal levels.
Analyzing historical usage data, global trends, and maintenance schedules, predictive analytics calculates the ideal PAR levels for each part.
For example, if a part historically requires six units on hand for consistent usage but you currently have 12 in stock, the system flags the excess inventory and recommends immediate action. This might include prioritizing the oldest stock for usage before expiration, redistributing surplus inventory to other locations, or selling unneeded parts to recover costs.
Transforming data into actionable insights
Predictive analytics doesn’t stop at setting PAR levels—it also provides actionable insights. ePlaneAI’s AI assistant, Aerogeny, continuously monitors inventory and operational data, offering recommendations based on real-time conditions. For instance, Aerogeny can:
- Alert you to upcoming demand spikes due to seasonal maintenance or increased flight schedules.
- Highlight parts nearing expiration or obsolescence, prioritizing their use or sale.
- Suggest optimal reordering quantities and timelines to avoid both overstocking and stockouts.
These insights empower aviation companies to take proactive steps, aligning inventory practices with operational needs while minimizing waste.
Integration with ERP systems
With PAR levels established and real-time insights generated, seamless integration with ERP systems like SAP and Oracle ensures that inventory, supply chain, and business data are consolidated across all locations.
This integration simplifies workflows and ensures all stakeholders have access to accurate, up-to-date, single-source information. With tools like Aerogeny, actionable insights are directly tied into ERP platforms, making it easier to align strategic decisions with day-to-day operations.
How ePlaneAI enhances real-time inventory management
By combining predictive analytics with ERP integration, ePlaneAI ensures inventory actions are unified and efficient. With features like precise PAR level setting and the ability to flag slow-moving parts, ePlaneAI transforms data into actionable strategies, streamlining stock management across your organization.
Purpose-built for aviation, ePlaneAI leverages AI-driven analytics and real-time tracking to optimize stock holding and automate critical inventory processes.
Here’s how ePlane delivers results:
- Predictive inventory alerts
ePlaneAI’s system continuously monitors stock levels, usage rates, and relevant external trends, sending predictive alerts for parts at risk of stockout, expiration, or obsolescence. This ensures maintenance teams can plan ahead, avoiding disruptions and unnecessary storage costs. - Integration with ERP systems
ePlaneAI integrates with all leading ERP platforms like SAP and Oracle, allowing aviation companies to consolidate inventory, supply chain, and business data across all locations. With this integration, companies can simplify workflows, ensuring all stakeholders have access to accurate, up-to-date, single-source information. - Tailored solutions for aviation
Unlike generic inventory management tools, ePlaneAI’s platform addresses the unique demands of aviation, from AOG emergencies to regulatory requirements for specific parts. Its aviation-focused approach ensures that companies get actionable insights and measurable ROI from day one.
Revamp inventory management with real-time alerting
Effective inventory management is a balancing act, especially in aviation, where stockouts and excess inventory can disrupt operations and drain resources, triggering a catastrophic domino effect. Real-time inventory systems, powered by AI and predictive analytics, give teams the tools to navigate industry challenges with precision and confidence.
ePlaneAI’s AI platform provides aviation companies with the insights and control needed to optimize inventory, avoid disruptions, and maintain fleet readiness. Whether it’s preventing stockouts with predictive alerts or reducing excess inventory through dynamic tracking, ePlaneAI ensures that critical components are in the right place, at the right time.
TIME TO ACT IS NOW
Ready to eliminate costly inventory disruptions? Aviation companies all around you are using AI to better manage their inventory. Don’t get left behind. Discover how ePlaneAI’s real-time inventory management solutions keep your inventory optimized and planes in the air. Visit ePlaneAI.
FAQs
What is CFM inventory?
CFM inventory refers to the inventory managed using continuous flow manufacturing (CFM) principles, a methodology designed to streamline production and inventory processes by minimizing waste, inefficiencies, and interruptions (Propel Software).
While real-time inventory management focuses on tracking stock levels as they change, CFM takes this further by emphasizing the continuous and synchronized flow of materials to meet production demands.
In aviation, CFM inventory is critical for maintaining a steady supply of parts and components. Platforms like ePlaneAI can effectively support and enhance CFM inventory practices in aviation.
What is a VMI system?
Vendor managed inventory (VMI) systems allow suppliers to monitor and manage inventory levels on behalf of their customers (Adobe). In aviation, a VMI system ensures that parts like turbine blades or avionics are always stocked to meet customer demand without requiring manual reordering. This reduces administrative overhead and ensures timely replenishment.
For example, ePlaneAI integrates with VMI systems to automate stock replenishment workflows, improving operational efficiency and reducing the risk of stockouts.
What system is used by airlines to keep track of their inventory?
Airlines use integrated enterprise resource planning (ERP) systems that are customized to handle the demands of passenger travel and air transportation. These systems often incorporate aviation software tools.
By combining ERP functionality with advanced, industry-specific tools, airlines can monitor inventory levels in real-time, track usage rates, and forecast demand accurately. This ensures that critical spare parts are available at the right time and location. Additionally, features like automated replenishment and predictive analytics further streamline inventory management processes.
What’s the difference between real-time inventory and JIT manufacturing?
Real-time inventory uses technology like AI to continuously monitor stock levels, providing up-to-the-minute updates to prevent stockouts or overstocking. JIT (Just In Time) manufacturing is a lean production strategy that minimizes inventory by ordering or producing only what’s needed, when it’s needed (Harvard Business School).
While real-time inventory focuses on optimized or automated stock management, JIT aims to eliminate excess stock entirely. Together, they balance precision with efficiency for fleet readiness without unnecessary costs.