Why Global Supply Chain Visibility Matters for Aviation Inventory Management
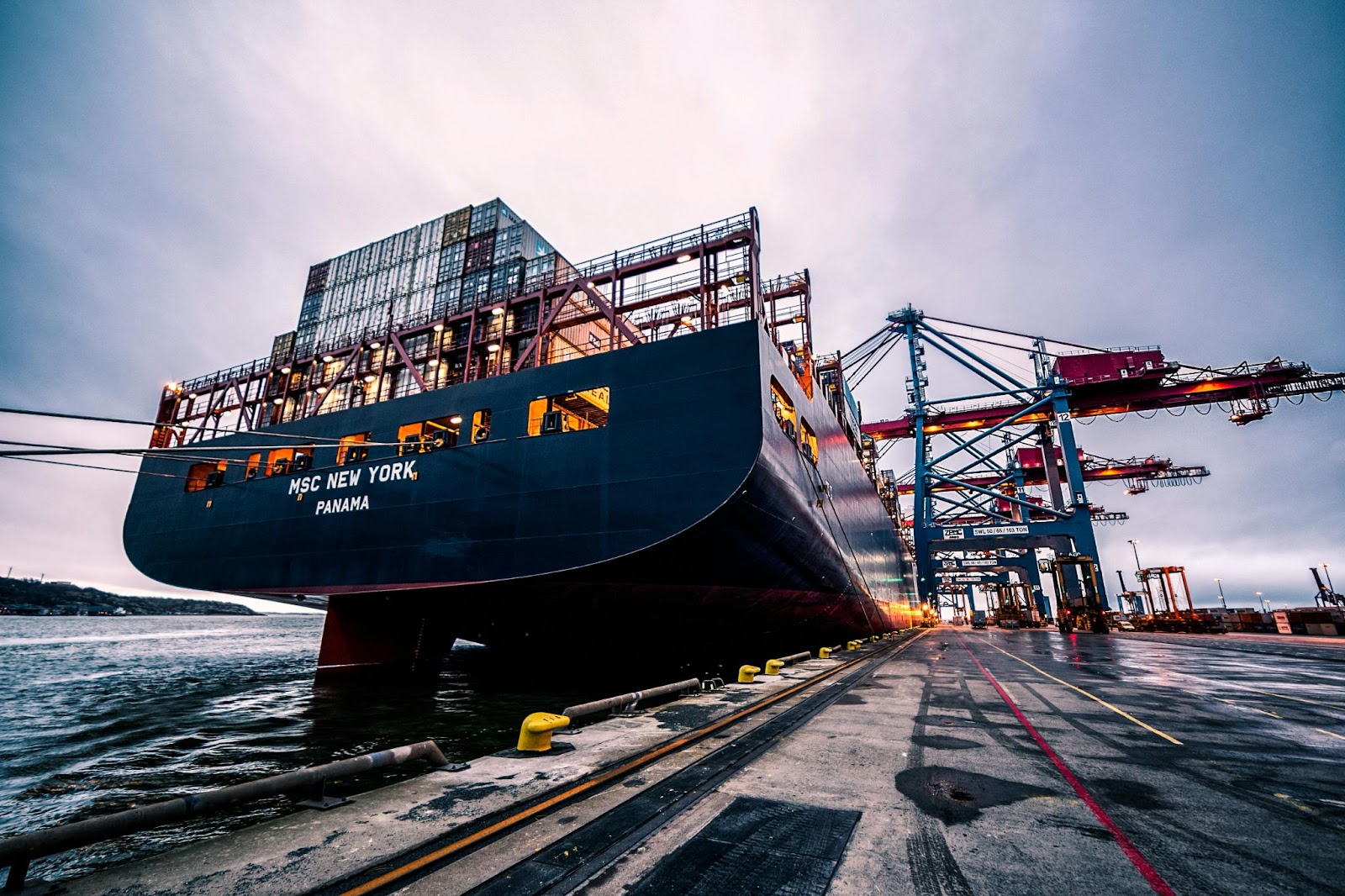
Supply chain visibility is no longer optional
In aviation, supply chains have never been more challenging to keep tabs on. Manufacturers, distributors, and customers span the globe, using different software systems and adhering to different government regulations.
Strongly interconnected, a single untracked party can disrupt entire flight schedules, compromise safety, and bring the global aviation industry to its knees. Every year, poor visibility into the global supply chain results in delays, grounded aircraft, lost company trust, and even regulatory fines.
Operations have mostly recovered from COVID-19
The global supply chain has undoubtedly made significant progress in recovering from pandemic-era disruptions, but it has not fully returned to pre-COVID conditions across all sectors.
The aviation industry, still recovering from COVID-era supply shocks, now faces renewed turbulence: surging passenger flight demand, aging fleets, and widespread supplier constraints. Some industries, such as technology and pharmaceuticals, have largely rebounded, while other industries, especially those reliant on region-specific manufacturing, face persistent challenges.
Key areas that have lagged in broader supply chain recovery:
- Shipping and logistics: Shipping delays and container shortages have improved, but congestion at key ports remains a concern.
- Labor shortages: Many industries are still struggling with labor shortages, especially in logistics, warehouse operations, and truck drivers, affecting the smooth flow of goods.
- Semiconductor shortages: Ongoing shortages in semiconductors have impacted the automotive and electronics industries, slowing production.
- Raw material shortages: Global demand for raw materials has increased, and supply is still lagging in some cases, especially with materials like steel, timber, and energy.
(Sources: Xeneta: The Biggest Global Supply Chain Risks of 2025, McKinsey & Company: Supply chains: Still vulnerable)
These lingering shocks have a direct impact on the aviation industry, as materials like aluminum, titanium, and steel are essential for aircraft construction and critical components (Government Accountability Office: Commercial Aviation Manufacturing: Supply Chain Challenges and Actions to Address Them).
Similarly, semiconductor shortages have severely affected avionics and aircraft electronics, leading to delays in manufacturing and repairs. These chips are crucial for systems such as navigation, communication, and in-flight entertainment (Glotronic: Soaring Above Challenges: How the Aviation Industry Navigates the Global Semiconductor Landscape in 2024).
Perhaps most significantly, labor shortages are a major challenge in the aviation supply chain, with critical roles such as aircraft mechanics, avionics technicians, and warehouse workers in short supply and AI technology upending legacy job roles and creating new staffing needs (Aviation International News: Supply-Chain Issues Continue to Roil Aviation Industry).
Walking an inventory tightrope
These lingering challenges have inventory teams walking a tightrope—balancing between cost control and maximal flight time—with minimal room for error. Visibility into every layer of the supply chain—across vendors, geographies, and transportation modes is the difference between resilience and chaos.
Internal industry observations concur. In 2024, 90% of supply chain leaders reported experiencing disruptions, yet fewer than 30% said their boards deeply understood those risks (McKinsey & Company: Supply chains: Still vulnerable). Meanwhile, maintenance demands are rising sharply as airlines delay aircraft retirements and stretch the lifespan of aging fleets.
If global visibility isn’t baked into your supply chain now, it’s time to catch up.
The unique challenges of aviation inventory management
Mission-critical parts and high complexity
Aviation inventory is like no other. It’s not just about keeping stockpiles of extra products; it’s about ensuring that you have the exact right part. Full traceability and airworthiness documentation must be available at beck and call, whenever and wherever needed.
The consequences of missing a spare part or required document are far more severe than in most industries: Grounded aircraft, delayed flights, regulatory penalties, and cascading operational costs.
This complexity is compounded by the types of parts involved and how these parts must be stored, maintained, and monitored.
Rotables (repairable items like landing gear and avionics) must be tracked over multiple lifecycles. Expendables (non-repairable, single-use items) still require careful logging and replacement forecasting. Every item must comply with strict regulatory oversight, and supply teams must manage millions, if not billions, of SKUs across global fleets.
Inventory managers must manage stock numbers, costs, and procurement logistics, along with regulatory risk, unpredictable demand, and the ever-present threat of AOG (aircraft on ground) events. In this environment, real-time visibility is the best way to make timely, safe, and efficient decisions.
Rising demand, shrinking slack
The aviation industry is booming again, but now with fewer new planes rolling off the line. A record-high backlog of over 16,000 aircraft orders means airlines are extending the life of their current fleets (McKinsey & Company: What does the future hold for commercial-aviation maintenance?).
Retirement rates are down 24% compared to pre-pandemic levels, which increases the volume and urgency of required maintenance work (McKinsey & Company: What does the future hold for commercial-aviation maintenance?). At the same time, the average commercial aircraft age has reached historic highs—14.8 years as of 2024—and older aircraft need more frequent servicing (Forbes: Airplanes Average 14.8 Years Old. Frontier Airplanes Average 4.6 Years). With fewer retired planes, there’s also a scarcity of used serviceable material (USM), which many airlines rely on to lower MRO costs.
This double bind—aging fleets and limited feedstock—makes proactive inventory planning harder than ever. Without global supply chain visibility, aviation teams are flying blind in a turbulent market.
How visibility supports better MRO outcomes
Servicing more with less: The aging fleet challenge
The global MRO (maintenance, repair, and overhaul) is being battered by a new wave of demand. With airlines deferring aircraft retirements and stretching existing assets longer, maintenance volume is rising fast. From 2024 to 2026, retirement rates are expected to be lower than the pre-pandemic average, while overall MRO spending is projected to climb 1.2% annually through 2034, hitting $135 billion (McKinsey & Company: What does the future hold for commercial-aviation maintenance?).
But here’s the catch: Next-generation aircraft entering fleets over the next decade require less frequent maintenance. This means today’s spike in MRO activity is largely a short-term surge tied to an aging fleet.
MRO providers and airline teams need direct, transparent access to supply chain operations so they can effectively pivot, meeting today’s high-touch needs with tomorrow’s lower-demand forecasts.
Supply chain visibility gives stakeholders the ability to monitor MRO inventory levels, forecast usage rates, and match part availability with optimal aircraft maintenance windows. When paired with AI and predictive analytics, it allows for smarter parts pooling, better lead-time estimates, and fewer surprises in the hangar.
Reducing AOG time and maintenance delays
An aircraft stuck on the tarmac awaiting a part is a disaster for both customer experience and cascading operational delays. Each AOG event costs airlines tens of thousands of dollars per hour in lost revenue, passenger compensation, and crew rebooking—and broader ripple effects across tightly scheduled routes.
Real-time supply chain visibility helps anticipate these breakdowns before they happen. With tools like digital twins and predictive AI models, airlines and MROs can simulate multiple maintenance scenarios, reroute parts proactively, and adjust flight schedules based on real-time part availability.
A McKinsey case study found that a commercial aerospace OEM using predictive analytics and early-warning systems reduced component shortages by 25% (McKinsey & Company: Addressing continued turbulence: The commercial-aerospace supply chain).
Digital twins and predictive tools are changing the game
What digital twins actually do
Think of digital twins as virtual replicas of your supply chain, warehouse, or maintenance operations. These aren’t static dashboards; they’re dynamic simulations powered by real-time and historical data. A digital twin predicts how inventory will withstand under different scenarios: shifts in demand, supply disruptions, weather events, or part failures.
When integrated with existing supply chain management (SCM) tools, like warehouse or transportation management systems, digital twins act like an AI-powered brain sitting on top of a company’s technology stack. The twins offer up-to-the-minute guidance on where to shift inventory, which shipments to expedite, or how to reallocate safety stock.
The results are staggering. Aviation businesses using digital twins have seen up to a 20% improvement in on-time delivery, a 10% reduction in labor costs, and a 5% revenue boost (McKinsey & Company: Digital twins: The key to unlocking end-to-end supply chain growth).
From predictive to prescriptive: Automating smart decisions
Digital twins provide critical guidance, shifting operations from reactive to preventative. For example, instead of waiting for a part to run low, AI models tied to digital twins can trigger reorder points based on current fleet utilization, seasonal flight patterns, or supplier reliability.
Airlines can, therefore, shift from “just-in-case” inventory stocking to leaner, smarter systems. In one McKinsey example, a global OEM used a digital twin to optimize outbound logistics and cut freight and damage costs by 8% (McKinsey & Company: Digital twins: The key to unlocking end-to-end supply chain growth).
The cost of poor visibility in a fragile supply chain
Preventing chaos at hidden, subiter supplier levels
Aircraft OEMs and MRO providers continue to face regular material shortages, delays in castings and forgings, and global bottlenecks for everything from semiconductors to electronics components. These shortages derail delivery timelines and inflate costs across the board.
Visibility gaps—especially into subtier suppliers—mean organizations are often blindsided by issues several tiers deep, where disruptions can lurk undetected until it’s too late.
In one case, a company that mapped sub-tier vendors discovered critical chip suppliers affecting production throughput. Once addressed, throughput increased by 45% (McKinsey & Company: Addressing continued turbulence: The commercial-aerospace supply chain).
This gain shows why surface-level visibility isn’t enough. The deeper your insight goes, the better you can preempt stockouts, shipping delays, and costly downtime.
The price of ad hoc decision-making
When supply chain data is scattered, outdated, or siloed, decision-making slows down—or worse, grinds to a halt. McKinsey’s 2024 supply chain resilience survey found that only 25% of boards discuss supply chain issues regularly, and just 9% of companies are compliant with new deep-tier transparency regulations (McKinsey & Company: Supply chains: Still vulnerable, Ecovadis: The EU Corporate Sustainability Due Diligence Directive (CSDDD) And The Evolving Regulatory Landscap).
Today’s firefighting-style inventory management might buffer many problems, but it doesn’t scale—and it certainly doesn’t reduce costs.
Smarter planning enables faster recovery from disruption
From ad hoc fixes to systems that self-heal
Recovery from a supply chain disruption should be measured in hours, not weeks. Yet, on average, it still takes companies two full weeks to respond effectively to major disruptions (McKinsey & Company: Supply chains: Still vulnerable). That lag is catastrophic in the aviation world.
Aerospace companies investing in predictive systems and real-time monitoring can dramatically cut recovery times. Tools like early-warning systems, AI-assisted planning, and simulation modeling give organizations foresight into delays and real-time levers to adjust schedules, reroute inventory, or escalate procurement.
Aerospace firms using digital supply chain twins and advanced planning systems have reported reductions in logistics bottlenecks, smoother manufacturing flows, and more efficient inventory turns (McKinsey & Company: Using digital twins to unlock supply chain growth).
AI doesn’t work without the right data
Artificial intelligence is powerful, but only if it's fed accurate, current, and comprehensive data. McKinsey's research shows that companies deploying AI-based APS systems (advanced planning and scheduling) often fall short because only 10% have fully deployed these systems, and many are still floundering with how to make use of the technology (McKinsey & Company: Supply chains: Still vulnerable).
The 80/20 rule applies: Most value comes from just getting started with reasonably good data. In the aviation sector, this could mean integrating maintenance data with parts sourcing platforms or connecting flight schedules with supplier order cycles.
Adopt visibility that drives performance
Creating a living, breathing map of your supply chain
Digital twins—real-time, AI-enhanced replicas of supply chain processes—are no longer a futuristic pipedream. These powerful models simulate inventory flow, forecast demand shifts, optimize warehouse utilization, and test what-if scenarios before they become expensive realities.
For aviation companies juggling parts distribution across hangars, MRO facilities, and global suppliers, digital twins offer a unified control tower.
Integrating predictive insights into existing tech stacks
Digital twins don’t require tearing down your existing tech stack. They integrate with traditional supply chain software like WMS, TMS, and APS tools to enhance data quality and decision-making rather than replacing existing systems that work.
Leading aviation firms are using this setup to dynamically adjust SKU-level safety stock, reroute shipments around weather disruptions, and predict surcharges before they hit.
Such predictive visibility is becoming the new cost of doing business globally.
Why inventory visibility is mission-critical in aviation
Aviation has always demanded precision. But as demand grows, fleets age, and global disruptions multiply, inventory management can no longer afford to be opaque or reactive.
True visibility means knowing not just what you have and where it is, but also what’s coming, what’s late, what’s risky, and what can be done now so operations continue without interruption.
The tools are here: AI, digital twins, early-warning systems, and predictive analytics. What’s needed next is a mindset shift—a commitment to deeper global insights and cross-functional collaboration for true resilience.
Ready to enhance your supply chain visibility and improve aviation inventory management?
Partner with ePlaneAI today and take control of your supply chain with cutting-edge predictive technology.