How to Manage Aviation Inventory More Efficiently with Integrated Inventory Management Systems
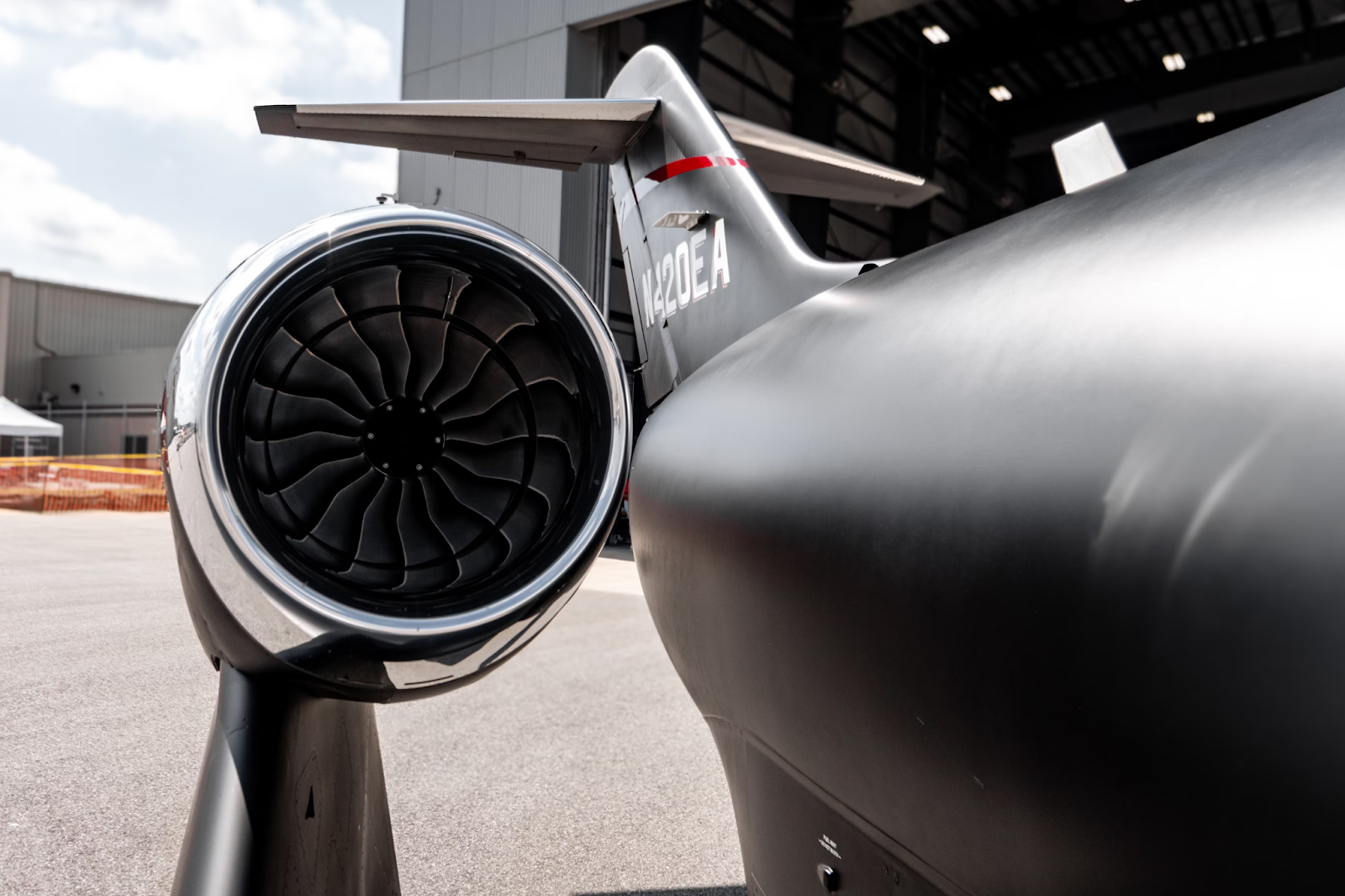
In the aviation industry, precision is everything. Downtime caused by stockouts affects more than profitability. It grounds planes, delays critical shipments, and disrupts people's lives.
At the same time, excess inventory ties up working capital and increases storage costs, leaving businesses with obsolescent parts and other inefficiencies that are hard to ignore. Real-time inventory management is the solution, enabling companies to optimize stock levels while ensuring availability when it matters most.
When aviation businesses leverage technologies like AI-driven inventory management, they can balance these competing priorities and remain competitive in a high-stakes market. This article will explore how real-time inventory systems prevent stockouts, reduce excess inventory, and drive operational excellence.
Understanding the challenges of stockouts and excess inventory
Stockouts: Costly operational disruptions
Stockouts occur when items critical to operations like spare parts, are unavailable at the time of need. For MROs, this can mean delayed repairs, grounded aircraft, or failed contract deadlines.
Even a brief stockout can snowball into significant operational setbacks, especially when dealing with high-cost parts and tight schedules. In an industry where every hour counts, the financial and reputational consequences are severe.
Unplanned downtime caused by stockouts can escalate quickly in the aviation industry, with losses climbing every hour for prolonged incidents. Beyond the financial burden, stockouts damage customer trust, strain supplier relationships, and disrupt broader supply chains. According to a study from McKinsey, supply chain disruptions caused by stockouts can reduce gross margins by 10%–20% (McKinsey).
Excess inventory is the capital killer
While maintaining high stock levels may seem like a natural buffer against stockouts, excess inventory has its own consequences for the aviation industry.
Slow-moving or obsolete parts tie up cash, take up valuable storage space (and incur storage fees), and increase the risk of waste due to expiration or regulatory constraints. For aviation companies, these issues are compounded by the specialized and often high-cost nature of aircraft components.
Cost of holding excess inventory
Excess inventory can represent a substantial financial burden. According to one manufacturing report (often cited in blog articles), carrying costs—such as storage, insurance, depreciation, and obsolescence—can account for 20% to 30% of the total inventory value.
It's particularly problematic for aviation businesses, where parts such as avionics, landing gear, or turbine blades can cost hundreds of thousands of dollars.
The aviation industry faces steep costs from obsolescent inventory. For just military aircraft alone, McKinsey estimates obsolescent inventory costs range from $50 billion to $70 billion.
Role of real-time inventory management systems
Real-time inventory management systems address these challenges by providing continuous visibility into inventory, including usage, customer demand, and product shelf life.
For example, ePlaneAI’s Inventory AI uses predictive analytics flags slow-moving parts and recommends actions such as redistribution to other locations or strategic resale to avoid obsolescence. It can auto-reorder commodity parts within certain price ranges when inventory levels fall below a set threshold, and it can automatically adjust PAR levels based on demand, activity level, seasonality and many other factors. This proactive approach helps companies free up storage space, recover capital, and focus on more critical inventory needs.
Role of real-time inventory management in aviation
Real-time inventory systems provide to-the-minute visibility into stock levels, enabling companies to stay ahead of demand or supply chain challenges. Businesses can streamline supply chain management processes when they integrate AI with their ERP to proactively analyze and manage inventory levels.
Preventing stockouts with real-time inventory
1. Accurate demand forecasting
AI-powered forecasting tools analyze historical usage patterns, real-time demand, and external variables like seasonality or supply chain delays. As a result, businesses can maintain adequate physical inventory levels without overstocking.
ePlaneAI’s inventory automation platform, Inventory AI uses predictive analytics to forecast demand spikes during peak travel or package seasons, ensuring the availability of critical components.
2. Inventory alerts for proactive replenishment
Real-time inventory management software provides alerts to notify teams when stock levels drop below predefined thresholds. These notifications ensure timely reordering, minimizing the risk of stockouts. Aviation companies can also configure alerts for specific high-priority parts, such as those critical for AOG scenarios, where downtime is most costly.
3. Supplier coordination and faster replenishment
When companies integrate inventory management systems with supplier networks, they can reduce lead times for replenishment. ePlaneAI’s platform facilitates seamless, immediate communication between aviation businesses and their suppliers, including automated reorder workflows to reduce lead times in the fulfillment process.
With automated inventory management systems, your order can be processed and prepared for shipment as soon as stock levels hit predefined thresholds, ensuring rapid replenishment while others are still manually checking inventory and calculating reorder needs.
Reducing excess inventory with real-time tools
1. Optimizing inventory levels
With real-time tracking, companies can avoid overstocking by analyzing current demand and usage patterns. For instance, Inventory AI adjusts inventory dynamically, helping aviation companies maintain the correct PAR level and reduce holding costs.
2. Identify and liquidate slow-moving items
Real-time systems can flag slow-moving or obsolescent items, allowing companies to take corrective action. For example, they could put the items up for sale in a marketplace, initiate promotional campaigns, bundle slow-moving items with high-demand parts, or reallocate inventory across locations. Thisfrees up both storage space and capital.
Additionally, AI working with data in your ERP system can help forecast how long a given part will be in production before OEMs cease production. They can monitor many external factors that impact manufacturing processes, including safety regulations, technology advances, and supply chain disruptions such as the inability to source raw materials.
3. Minimizing waste
In aviation, many components have a limited shelf life or regulatory constraints on their usage. Real-time tracking ensures that these items are used before expiration, reducing waste and compliance risks. Inventory AI can prioritize the allocation of time-sensitive parts to minimize losses.
Case studies: Real-world impact of effective inventory management
1. Aerospace manufacturer: Dynamic inventory optimization
An aerospace manufacturer struggled with high inventory costs, maintaining $600 million in surplus parts inventory for aircraft engines. They integrated an inventory tracking solution with their ERP system, which provided a real-time view of inventory levels and outlined supplier risks. This led to significant savings in inventory holding costs and improved service levels (IoT ONE).
2. DA Aviation: Smart inventory management solutions
A major Asian airline faced inventory challenges with its Power-by-the-Hour (PBH) component pooling program. This system lets airlines pay for parts and maintenance as needed, cutting the costs of stockpiling unused inventory. But creating such a program is no small task.
DA Aviation stepped in to support the airline’s tender (RFP and RFQ) processes. They streamlined supplier negotiations and structured a proposal that aligned operational demands with financial goals.
As a result of integrating its inventory management with suppliers and its PBH program, the airline was able to reduce inventory and associated carrying costs, ensuring parts are there when needed and not gathering dust on warehouse shelves.
How Inventory AI from ePlane transforms inventory management
Integrated inventory management requires precision, speed, and adaptability—qualities traditional systems often lack. ePlaneAI tackles these shortcomings with Inventory AI its flagship solution designed specifically for the aviation parts supply chain.
1. Predictive inventory monitoring
Inventory AI leverages AI to analyze historical data, real-time stock usage, internal business processes, and industry trends. This enables businesses to predict demand spikes and address inventory imbalances before they become problematic. For example, during peak travel seasons, ePlaneAI ensures that critical components, such as landing gear or avionics parts, are readily available. This proactive approach reduces downtime and prevents costly delays caused by stockouts.
2. Dynamic supplier coordination
Inventory AI enhances communication between aviation companies and their suppliers when they integrate with ERP systems like SAP and Oracle. The platform allows for real-time data sharing, allowing suppliers to be contacted automatically with an RFQ or PO when stock levels fall below certain thresholds. This eliminates manual intervention and shortens lead times, helping businesses fulfill AOG requests faster—a critical advantage in competitive markets where every second counts.
3. Optimize inventory utilization
Inventory AI goes beyond tracking stock levels. It provides actionable insights into how inventory is being used across multiple locations. For example, the platform can identify surplus parts at one hub while flagging shortages at another, enabling companies to redistribute resources effectively. This reduces excess inventory and eliminates unnecessary purchases, freeing up working capital for other priorities.
4. Real-time alerts for high-value components
In the aviation industry, where parts like turbine blades or engine components can cost hundreds of thousands of dollars, ensuring availability is non-negotiable.
ePlaneAI's real-time inventory alerts notify teams immediately when these critical components are running low or nearing expiration. By acting quickly and proactively on these alerts, companies can maintain optimal stock levels while avoiding overstocking.
5. Mitigate obsolescence risks
With AI-driven insights, ePlaneAI identifies slow-moving or at-risk inventory, such as parts nearing regulatory obsolescence or items for retired aircraft models. The platform recommends precise steps for cost savings, such as redistributing these parts, bundling them for sale, or offering targeted promotions to clear stock. This reduces waste and ensures businesses aren't left holding millions of dollars in unusable inventory.
6. Scalability for growing fleets
ePlaneAI’s modular architecture, which lets businesses add functions as needed, makes it ideal for businesses looking to scale their operations. Whether a company is expanding its fleet or adding new routes, the platform flexes to accommodate increasing inventory complexity and new ways to streamline your business.
Aerospace companies and aviation businesses can start with essential features like predictive analytics, demand forecasts, and inventory alerts, then scale up to additional capabilities as their needs evolve, such as supplier performance tracking and advanced maintenance scheduling.
7. Focused on aviation-specific challenges
Unlike generic inventory management solutions, ePlaneAI is tailored specifically to the aviation industry. The platform accounts for challenges unique to the sector, such as compliance with aviation regulations, the high value of stock items, and the logistical hurdles of maintaining global supply chains. This specialization ensures that ePlaneAI delivers a targeted solution that integrates smoothly with existing ERP and supply chain management (SCM) systems.
Steps to automate inventory management with AI
Implementing an automated inventory management system requires a strategic approach to ensure minimal disruption and maximum efficiency with early, measurable ROI.
While there's no one-size-fits-all approach, these are the general steps that businesses follow:
- Implement AI Inventory Automation
Leverage platforms like ePlaneAI that use advanced algorithms to optimize inventory management and unify real-time data across operations. This includes automatically pulling in data from suppliers, warehouses, and industry usage trends to deliver advanced forecasting and planning insights day-in-day-out. - Integrate with existing ERP system
Select an automated inventory management platform that can sync effortlessly with your existing ERP, OMS, and Email. When you combine all of these, it creates a single source of truth for data integrity, resulting in improved visibility, insights, and decision-making compared to siloed systems. - Set up alerts and dashboards
Set up real-time alerts and dynamic dashboards to track critical metrics across all your inventory locations. Integrated systems help you monitor stock levels, detect discrepancies, and respond to potential issues like supply chain disruptions or overages. - Train staff and standardize workflows
Teach your team how to use the new system inside out. Align workflows across departments to keep things consistent and make the most of the system’s features, like restocking inventory, managing suppliers, and automating previously manual processes.
Final thoughts
Integrated inventory management keeps your operation sharp. No waste. .No waiting. Parts flow where they’re needed, critical components are ready on time, and setup costs shrink. Informed decisions replace guesswork, backed by real-time data and lean manufacturing principles.
In aviation, where every minute matters, this approach isn’t just efficient—it’s essential. A short period of downtime can ground fleets and erode trust. But with the right system, you keep planes moving, customers happy, and profits steady. Success starts with precision. Success starts here with ePlaneAI.
Stay ahead of stockouts, cut excess costs, and transform your supply chain. ePlaneAI delivers efficiencies worth millions in months. Let us help you take control of your inventory. Book a meeting with ePlaneAI today.