How to Use Predictive Maintenance to Decrease Costs in Aviation
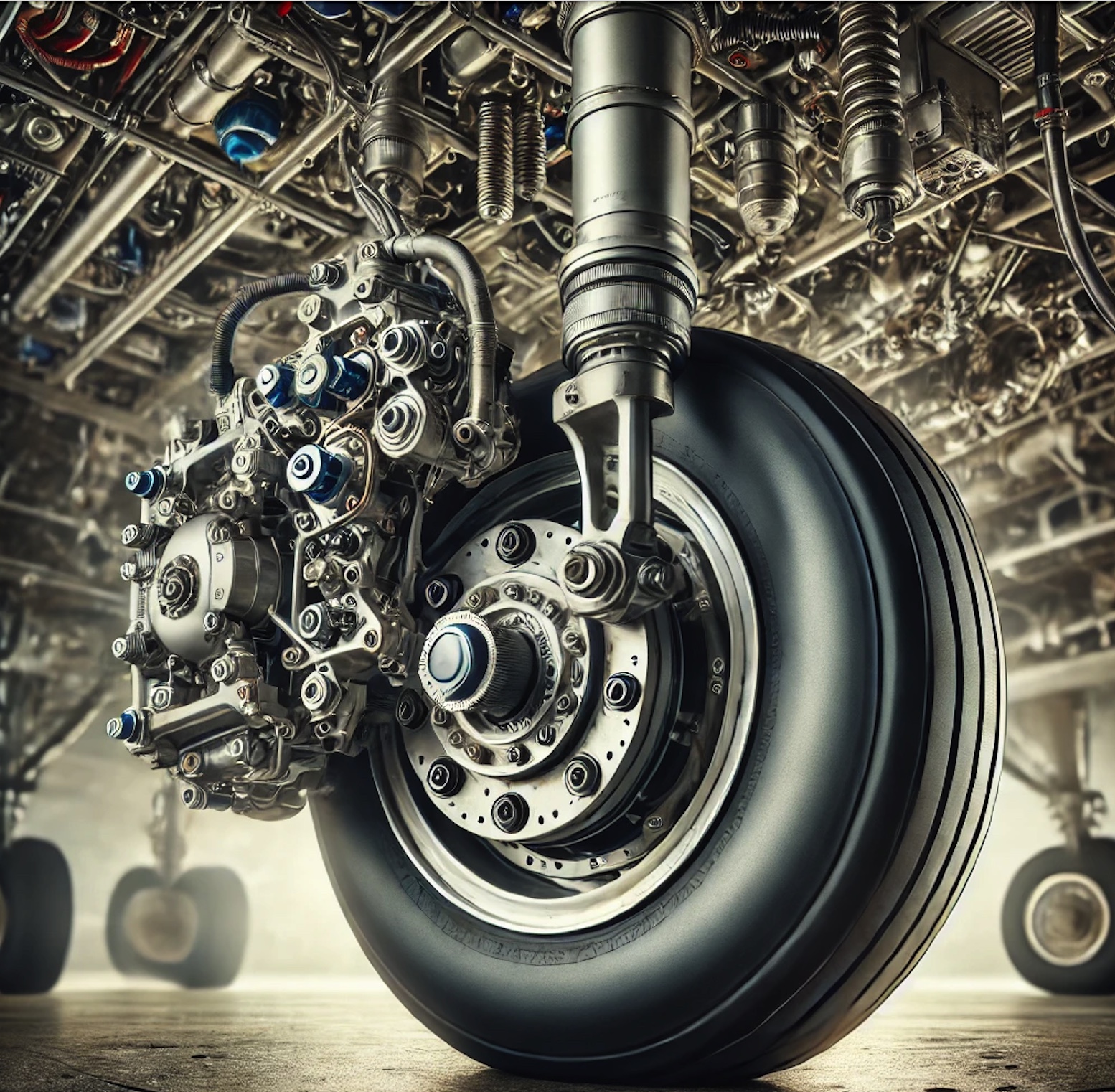
In aviation, every delay, even a single minute on the ground, costs money. Planes that should be in the air are often sidelined for repairs that could’ve been prevented. Yet, for decades, the industry has leaned on a mix of react and repair—fixing what breaks or swapping out parts on an 'optimized' schedule, hoping to avoid trouble.
While routine maintenance can help, there’s definitely a smarter, more efficient way to manage part replacements when you can use performance data from the parts themselves, to help you quantify the risk of failure and predict the best time to swap out the part. This is the science of predictive maintenance.. Predictive maintenance keeps planes in top shape by anticipating—or 'predicting'—issues before they become severe enough to ground aircraft.
What is aircraft predictive maintenance?
Predictive maintenance is a proactive approach to aircraft upkeep. Unlike traditional maintenance, it uses real-time data and historical trends to predict when certain parts might fail or require upgrading. Sensors monitor critical components in real-time, proactively looking for potential issues so they can be immediately addressed. This reduces aircraft downtime and avoids the resource drain of unexpected parts and premature part replacements.
What is predictive maintenance vs. preventive maintenance?
Aircraft preventive maintenance follows a fixed schedule, such as A-checks, C-checks, and D-checks, where parts are inspected or replaced after a set amount of time or usage, regardless of their condition. These checks aim to prevent equipment failure but can also lead to replacing parts that are still functional, resulting in unnecessary expenses. Think routine oil changes, engine tune-ups, and regular inspections of landing gear or flight control systems. When technicians perform preventive maintenance, they aim to prevent equipment failure, but it can also lead to replacing parts that are still 'good,' resulting in unnecessary part replacement and added labor costs. And not replacing ones that may have had excessive wear for some reason, but according to the schedule is not due yet… this increases risk.
Predictive maintenance, by contrast, is a form of preventive maintenance that is data-driven and condition-based. By analyzing real-time data from sensors, it identifies only those parts that actually need attention. This targeted approach not only saves on costs but also minimizes downtime, keeping aircraft flight-ready with greater efficiency.
How predictive maintenance in aviation works
For aircraft fleets, predictive maintenance uses several technologies to surveil equipment and monitor for component wear.
Primary technologies to perform predictive maintenance include:
IoT sensors
Internet of Things (IoT) sensors are installed on critical aircraft parts like engines, landing gear, and hydraulic systems. These sensors capture data on temperature, pressure, vibration, and other parameters.
Data analytics
Once captured, the data is analyzed using algorithms that look for trends and patterns linked to component failure. For example, an engine vibration data log could reveal that certain fluctuations mean an 80% probability of engine failure within X hours. Here, technicians are alerted so they can include the needed repairs at the next maintenance. Hence, with proper preparation and good inventory management, the need for additional aircraft downtime beyond the scheduled maintenance can be avoided.
Machine learning (ML) and AI
Machine learning algorithms enhance the predictive maintenance process by continuously learning from past data, improving accuracy over time. AI-powered platforms can spot nuanced patterns across vast data sets and detect failure indicators that human analysts and technicians would not be able to discover in time.
Digital twins
Digital twin technology, which creates a virtual model of the aircraft or its components, allows operators to simulate the impact of various conditions on part longevity. This makes it possible to predict 'wear and tear' more accurately by factoring in What-if scenarios such as environmental conditions or operational patterns.
Benefits of predictive maintenance for aviation companies
The advantages of predictive maintenance extend far beyond simple cost savings. Here are several key benefits:
- Reduced maintenance costs: By catching minor issues before they escalate, predictive maintenance prevents costly, major repairs and extends the life of components.
- Increased aircraft availability: Fewer unplanned repairs mean aircraft spend less time on the ground, improving fleet utilization and flight volume.
- Enhanced safety: Predictive maintenance catches potential failures so technicians can perform maintenance before issues become critical, reducing the risk of in-flight safety issues.
Better compliance and documentation: Predictive maintenance platforms often come with built-in compliance checks, making it easier to meet Federal Aviation Administration (FAA) and other industry regulations by automatically logging maintenance activities and inspection data.
Key challenges of implementing predictive maintenance
While predictive maintenance offers many benefits, it also comes with many considerations and challenges.
Data integration
Predictive maintenance relies on data from numerous sources, such as engine propellers, auxiliary power units, landing gear, and avionics. Onboard IoT sensors and systems, like the aircraft’s black box, collect parameters such as temperature, pressure, and vibration in real-time.
This data is transmitted wirelessly to servers or cloud platforms, where it’s aggregated, cleaned, and formatted for AI and machine learning analysis. These systems identify trends and anomalies, signaling potential issues before they escalate.
Integrating such data can be challenging for legacy systems, often requiring updates or specialized solutions to enable seamless real-time analytics.
Upfront investment
Setting up predictive maintenance infrastructure—purchasing IoT devices and sensors, implementing AI software, and training staff—can be costly. For smaller aviation companies or MRO (maintenance, repair, and overhaul) providers, these initial costs may make predictive aircraft maintenance seem prohibitive, although the long-term savings can justify the investment.
Technical expertise
Predictive maintenance in aviation requires specialized skills in data analytics, machine learning, and IoT. Companies may need to partner with specialists like ePlaneAI, who can tailor AI solutions to your precise needs and deliver predictive insights through intuitive, actionable dashboards. These dashboards simplify complex analytics, enabling teams to make informed decisions without needing advanced technical expertise.
Data security
With IoT sensors transmitting data wirelessly, a predictive maintenance system can be vulnerable to cyber threats. Ensuring data security is pivotal, and aviation companies must establish robust security protocols.
Change management
Implementing predictive maintenance requires a shift in organizational mindset. Teams accustomed to preventive schedules may need to adapt to new methodologies for performing preventive maintenance. Ongoing training and a phased approach can help ease this transition.
Real-world examples and case studies
As the idea of predictive maintenance gains traction in aviation, industry leaders are showing how this approach can reduce costs and improve efficiency across maintenance tasks.
Airlines and manufacturers alike are using predictive tools to stay ahead of repairs, optimize complex operations, and keep aircraft safely in service. Below are some real-world examples that highlight the benefits of predictive maintenance in aviation.
Delta Air Lines
Delta Air Lines has taken the lead in predictive maintenance, using data analytics to improve critical maintenance tasks and minimize the need for major alterations or overhauls.
By applying predictive analytics to key systems, Delta has reduced unscheduled maintenance events, improved on-time performance, and reduced flight cancellations. The investment in predictive technology not only increases fleet reliability but also lowers costs by allowing aviation maintenance technicians to carry out MRO tasks with greater precision. This substantial improvement in reliability translates into considerable cost savings. While exact figures are proprietary, industry analyses suggest that predictive maintenance can lead to a 25% reduction in maintenance costs and a 20% increase in aircraft availability.
Applying these estimates to Delta's operations, with its annual maintenance expenditures exceeding $1.5 billion, implies potential savings in the hundreds of millions of dollars each year.
Airbus and the Skywise
Airbus’s Skywise platform is a standout example of predictive maintenance. Skywise collects real-time data from thousands of sensors on Airbus aircraft, analyzing everything from spark plug gap clearance to landing gear wheel bearings. This allows Airbus and its airline partners to detect maintenance needs early and address them proactively for fewer cancellations and safer aircraft.
GE Aviation’s predictive maintenance solutions
GE Aviation is advancing predictive maintenance by combining digital twin technology and IoT. GE’s system tracks critical components like engines and landing gear, using predictive insights to schedule maintenance efficiently. By identifying issues early, GE’s technology helps airlines maintain readiness and avoid unexpected downtime.
Best practices for implementing predictive maintenance
For predictive maintenance to deliver to its full potential, strategic planning is essential. Here are some best practices to help aviation companies successfully integrate predictive maintenance into their operations:
- Start with high-impact systems: Focus on critical systems—like engines and landing gear—that have the greatest impact on safety and operational readiness. Testing predictive maintenance here first can help demonstrate value and gain organizational buy-in.
- Prioritize training and skill development: Equip your team with the skills needed to interpret sensor data and manage predictive tools. Providing ongoing training ensures that technicians and engineers can make data-informed decisions with confidence.
- Collaborate with industry experts: AI and machine learning require specialized knowledge, especially in aviation and supply chain management. Partnering with experts like ePlaneAI ensures you’re working with a team that understands both AI technology and the unique demands of aviation. Unlike ERP systems, which were not designed for AI, ePlaneAI’s solutions are purpose-built extensions that integrate seamlessly with existing infrastructure while handling the complexities of AI data.
- Set measurable goals: Define clear KPIs, such as an X% reduction in unscheduled maintenance or maintenance costs, to track the effectiveness of your predictive maintenance program. Data-driven goals allow for continuous improvement and adjustment.
- Maintain robust cybersecurity: With the increased data flow from IoT devices, establishing strong cybersecurity protocols is critical to protecting sensitive aircraft data from potential cyber threats.
Implement predictive maintenance with ePlaneAI
For aviation companies wanting to leverage to predictive maintenance, ePlaneAI offers a tailored, aviation-specific platform that streamlines operations and reduces downtime.
Minimize disruptions
With real-time monitoring, ePlaneAI continuously tracks systems across the aircraft—from engines to auxiliary components. When potential issues are detected, maintenance teams receive alerts, enabling timely interventions that prevent escalation and minimize costly disruptions.
Automatic trend analysis
The ePlaneAI platform’s advanced analytics identify patterns in performance data, allowing teams to address specific maintenance needs before they impact operations and avoid unnecessary replacements.
Seamless integration
The integration of this data flow is seamless with ERP and MRO systems, making predictive insights readily available in the systems and processes teams already use.
Reporting, simplified
Finally, automated compliance logging simplifies regulatory reporting. ePlaneAI records all maintenance activities in real time, reducing the administrative load and ensuring that each step meets FAA preventive maintenance standards.
Final thoughts
Predictive maintenance marks a shift in aviation, offering a smarter, more efficient approach to fleet management. By addressing potential issues before they surface, aviation companies can minimize downtime, reduce maintenance costs, and improve overall safety.
As an industry-leading Aviation AI solution provider, ePlaneAI enables aviation professionals to make predictive maintenance a practical, actionable strategy.
For companies ready to enhance their maintenance operations, ePlaneAI provides the tools and expertise to leverage predictive maintenance in your business. Partner with ePlaneAI to realize efficiencies worth millions.
FAQs
What are the four types of preventive maintenance?
Preventive maintenance covers various approaches to maintaining equipment and reducing the likelihood of unexpected failures. The four main types include:
- Time-based: Scheduled maintenance performed at set intervals (e.g., monthly or annually) regardless of equipment condition. This type aims to prevent failures by servicing parts on a regular schedule.
- Usage-based: Maintenance is conducted after specific usage milestones, such as flight hours, engine cycles, or mileage.
- Condition-based: Maintenance that relies on real-time monitoring of equipment health, often using sensors to track parameters like temperature, pressure, or vibration. Maintenance is performed only when data indicates deterioration.
- Predictive: A data-driven approach that forecasts maintenance needs by analyzing patterns from historical and real-time data. Predictive maintenance tools help anticipate failures before they occur, reducing downtime and extending component life.
Each of these preventive maintenance types brings unique benefits for cost, resources, and reliability, but predictive maintenance stands out for its powerful ability to continually analyze data and accurately predict the precise amount of predictive maintenance work needed.
Can a private pilot perform preventive maintenance?
Yes, a private pilot can perform certain preventive maintenance tasks on an aircraft, as authorized by the Federal Aviation Administration (FAA) under 14 CFR Part 43 (ECFR). These tasks are limited to minor operations, such as replacing spark plugs, cleaning filters, or changing hydraulic fluid, and must follow the guidelines in the aircraft’s maintenance manual.
What is 14 CFR Part 43?
14 CFR Part 43 is a section of the U.S. Code of Federal Regulations that governs the maintenance, preventive maintenance, rebuilding, and alteration of aircraft. It outlines the standards for aviation technicians and specifies what types of maintenance can be performed by authorized personnel, such as repair station certificate holders and pilots performing minor preventive tasks.
How does predictive maintenance differ from reactive maintenance?
Predictive maintenance is a proactive approach that uses data and analytics to predict and address potential issues before they cause downtime. In contrast, reactive maintenance involves addressing issues only after they arise, often resulting in unplanned repairs and increased costs. Implementing predictive maintenance programs means companies can reduce disruptions and improve asset reliability.
What to look for in predictive maintenance software?
Choosing the right predictive maintenance solution involves evaluating your specific operational needs and the capabilities of available tools. Here are a few key factors to consider:
- Data integration: Look for software that can integrate with your current systems, such as ERP, MRO, and asset management systems. Smooth integrations make for accessible insights into performance data without disrupting workflows.
- Analytics capabilities: The best predictive maintenance tools offer advanced analytics powered by AI and machine learning for more proactive insights into equipment health.
- User interface and ease of Use: Predictive maintenance software should have an intuitive interface that’s easy for technicians and users to navigate with clear dashboards and easy data visualization tools.
- Scalability and flexibility: As your operations grow, your predictive maintenance needs may evolve so it's best to choose software that is flexible and scalable, capable of adjusting to a growing fleet and evolving maintenance needs.
- Vendor support and training: Implementation needs hands-on training and steady backup. Choose a provider like ePlaneAI with solid guidance and resources you can count on.
- Aviation expertise: ePlaneAI specializes in aviation, offering tailored solutions to meet the industry’s unique demands, from real-time monitoring to AI-driven insights.