How AI Optimizes Inventory Rotation for Aviation Efficiency
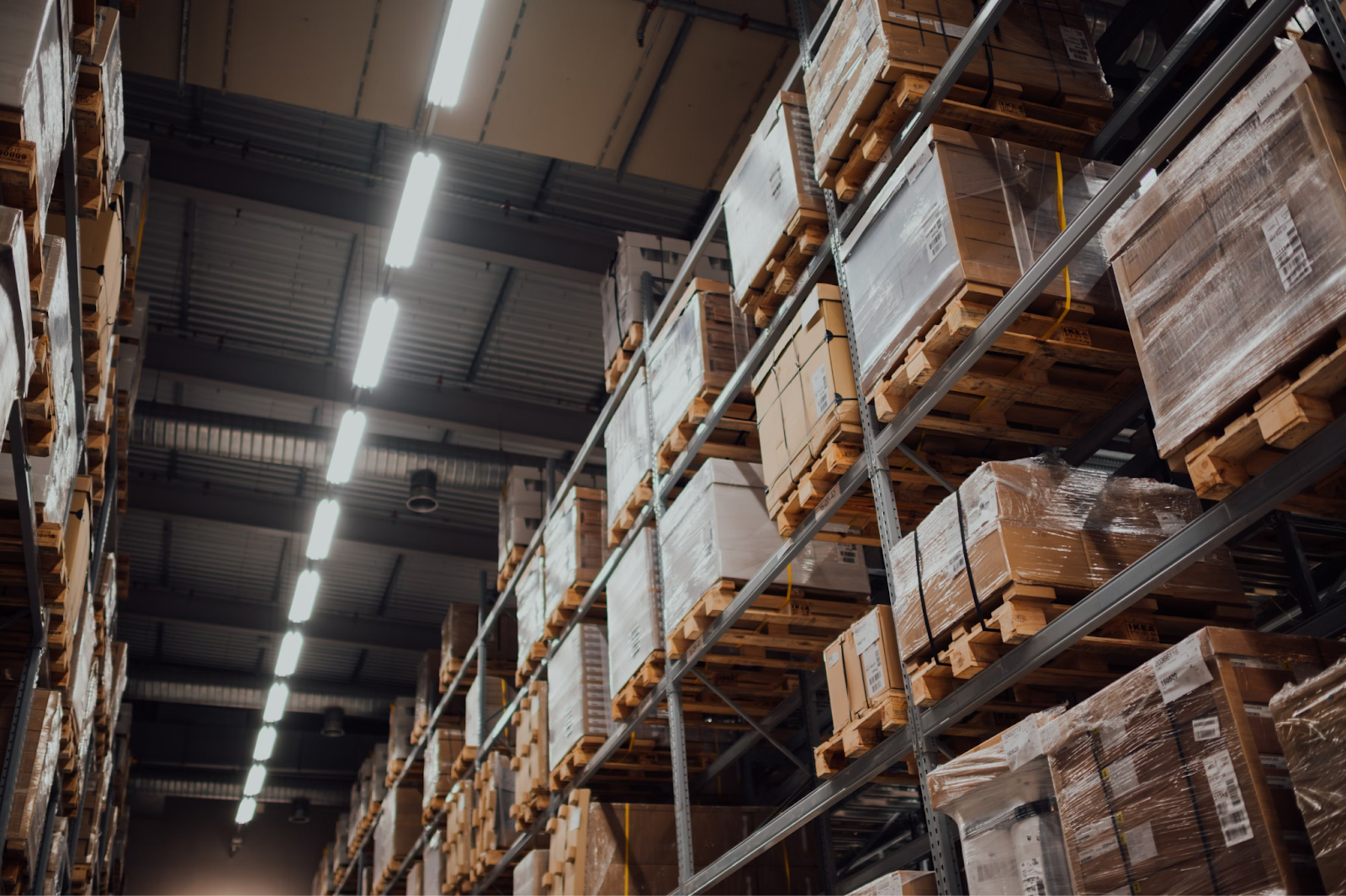
In the aviation industry, inventory management isn’t just about having the right parts—it’s about knowing their condition, rotation status, and usability. For aviation maintenance, repair, and overhaul (MRO) providers, this challenge is magnified by the complexity of parts with varying lifecycles and compliance standards.
AI, however, is bringing real-time, data-driven solutions to streamline inventory rotation and ensure operational efficiency.
What is inventory rotation?
Inventory rotation, as defined in a Naval Research Logistics (NRL) study, is the systematic process of managing inventory items' usage, replenishment, and lifecycle to ensure they are used efficiently, maintain quality, and align with operational needs.
A critical metric in this process is the inventory turnover ratio, which measures how often inventory is sold or used over a specific period. It’s calculated by dividing the cost of goods sold (COGS) by the average inventory, providing insight into how effectively inventory is being managed.
Efficient rotation minimizes waste, reduces holding costs, and ensures products remain usable. Businesses often rely on inventory management software to monitor stock levels, track item lifecycles, and forecast demand.
Inventory rotation in aviation
In the context of aviation, inventory rotation incorporates specific elements such as tracking the condition and shelf life of high-value or perishable components, ensuring compliance with regulatory bodies like the FAA or EASA, and aligning stock levels with fluctuating demand to minimize waste and operational downtime.
Unlike traditional inventory strategies, aviation inventory rotation focuses on conditions such as:
- Shelf-life-sensitive materials: Monitoring the condition of parts like tires, batteries, and other items that can degrade over time if not stored in optimal conditions.
- Time-limited components: Some items require rotation to comply with regulatory body directives.
- Usage tracking: Ensuring frequently used parts are replenished while rarely used ones aren’t wasted.
The FAA Inventory Management Guide highlights the importance of proper stock rotation and categorization to distinguish between recurring-demand items and expendable materials. AI tools can ensure such classifications are consistently managed, further enhancing inventory rotation effectiveness.
Poor inventory rotation doesn’t just waste resources—it can ground aircraft and lead to major safety concerns.
Adding to the challenge of inventory rotation is "lumpy demand," a phenomenon where the need for high-value rotatable components like engines and avionics is inherently unpredictable (POMS MacDonnell and Clegg).
Lumpy demand is characterized by irregular spikes in demand, driven by unexpected maintenance needs or unplanned events. These irregularities make it essential to adopt a highly strategic approach to maximize inventory efficiency.
Challenges of inventory rotation in aviation
Beyond lumpy demand, managing aviation inventory rotation presents other unique challenges:
- No traditional inventory turnover formula: Lumpy demand disrupts inventory rotation planning, requiring more adaptable systems. A conventional inventory turnover formula cannot be applied to calculate inventory turnover in an industry where needs are dynamic and changing by the minute.
- High-value parts and cost constraints: Average inventory value is astronomical. Rotating multimillion-dollar components like engines ties up significant capital, while consumables with finite shelf lives risk expiration, obsolescence, or non-compliance if not prioritized correctly.
- Decentralized storage complexities: Managing inventory across multiple facilities with varying demand patterns complicates consistent rotation, especially for slow-moving or high-value parts.
- Complex compliance: Strict regulations dictate when parts need inspection, replacement, or certification, adding pressure to maintain accurate records.
- Audit and traceability pressures: Lifecycle traceability and audit readiness create operational challenges, especially when relying on fragmented or manual systems.
- Data silos and manual processes: Disconnected systems for procurement, maintenance, and inventory hinder efficiency, while human oversight increases the risk of errors in monitoring and tracking.
These challenges make it clear why traditional methods often fall short—and where AI offers transformative solutions.
How AI brings more effective inventory part rotation
Artificial intelligence leverages advanced technologies like machine learning (ML), predictive analytics, and real-time data integration to optimize inventory rotation. Here’s how:
Monitoring part conditions
AI tools excel at analyzing the factors that influence part usability:
- Environmental conditions: Monitor storage environments, such as temperature and humidity, maintaining proper conditions to prevent material degradation.
- Performance and shelf-life tracking data: Real-time monitoring to track performance. AI flags parts close to expiration or requiring inspection.
- Predictive rotation planning: Analyze historical trends and operational data to determine the optimal timing for rotating parts, mitigating risks from irregular demand and stockouts.
- Lifecycle tracking: AI tools can track parts and their associated documents from procurement to disposal, ensuring compliance with FAA and EASA regulations and audit-ready records.
For example, a fleet operator using ePlaneAI’s Inventory AI might identify that specific oxygen masks stored in high-humidity environments are degrading faster than expected. The system can then prioritize those items for immediate rotation or replacement.
Aligning inventory with operational demand
AI provides a data-driven approach to matching inventory rotation with operational needs:
- Demand forecasting: Predictive models analyze flight schedules, seasonal trends, and historical data to anticipate customer demand and minimize excess inventory.
- Dynamic rotation: Instead of rotating based solely on fixed schedules, AI prioritizes parts based on real-time conditions and demand.
This ensures that high-usage items like filters or brake pads are replenished without delay, while less critical components aren’t overstocked.
Automating compliance
Meeting industry regulations requires meticulous recordkeeping and adherence to inspection schedules. AI simplifies compliance through:
- Real-time alerts: Systems notify teams when parts near required certification or replacement.
- Audit-ready documentation: AI tracks every stage of a part’s lifecycle, ensuring data is readily available for inspection.
- Proactive mitigation: AI prevents non-compliance before it becomes an issue by identifying high-risk parts.
For instance, an MRO using AeroGenie could generate automated reports showing that all rotated parts meet regulatory standards, making audits faster and less stressful.
These tools align closely with recommendations from the FAA for leveraging technology to enhance compliance and streamline operations.
How ePlaneAI’s tools optimize inventory rotation
ePlaneAI offers a suite of AI-powered solutions designed to address the most pressing challenges in aviation inventory management:
- Parts Analyzer: Focuses on external factors by scouring the internet to gather data on global supply and demand for aviation parts. This tool identifies trends, anticipates price changes, and predicts supply shortages, enabling companies to plan rotations strategically around global market conditions.
- InventoryAI: Leverages predictive analytics to optimize inventory rotation internally, aligning stock levels with operational schedules and demand. It ensures high-usage components are always available, tracks part conditions, and flags inventory at risk of obsolescence, minimizing waste and downtime.
- AeroGenie: Integrates inventory data with compliance systems, ensuring all rotated parts meet regulatory requirements. It simplifies audits by providing real-time, accurate documentation for every stage of a part’s lifecycle.
Benefits of AI-powered inventory rotation
AI tools enhance inventory rotation by addressing inefficiencies and streamlining key processes. Real-time condition monitoring ensures inventory is used efficiently, preventing overstocking, obsolescence, and waste. Automated tracking systems simplify compliance, reducing regulatory risks and ensuring audits are faster and more accurate.
These tools also improve inventory turnover rates, accelerating the cycle of usage and replenishment to boost cash flow and reduce storage costs.
Smarter decision-making and efficient inventory rotation provide businesses with a clear advantage in managing the complex demands of aviation inventory management.
Getting started with AI for inventory rotation
To transform your inventory rotation strategy, begin by assessing areas where inefficiencies lead to waste, delays, or compliance risks. Document key resources, risks, and operational goals to identify where AI solutions can provide the most immediate value. This process ensures your efforts are laser-focused on high-impact areas.
Once you’ve established initial success, gradually expand AI implementation to additional inventory categories, integrating these tools into broader workflows. Partnering with experts like ePlaneAI ensures solutions are tailored to your unique operational demands, addressing your business’s most pressing challenges head-on.
Why starting small makes a big difference
AI isn’t an all-or-nothing approach. You don’t need a complete overhaul to see results—just a targeted effort in the right areas. Quick wins, like automating inventory monitoring or addressing one high-priority challenge, can show measurable value in weeks. These smaller, scalable steps build confidence in the power of AI while minimizing risk, helping you lay the foundation for sustained success.
The future of AI in inventory management
AI isn’t just the future—it’s the present. When competitors are already streamlining operations, cutting costs, and gaining an edge with AI, standing still isn’t an option. Solutions like ePlaneAI don’t just improve efficiency—they set the standard for survival in a competitive market.
Don’t wait while others gain the edge. Contact ePlaneAI today to see how our AI-powered solutions can redefine your inventory management strategy.