Preventing Inventory Shrinkage in the Aviation Industry
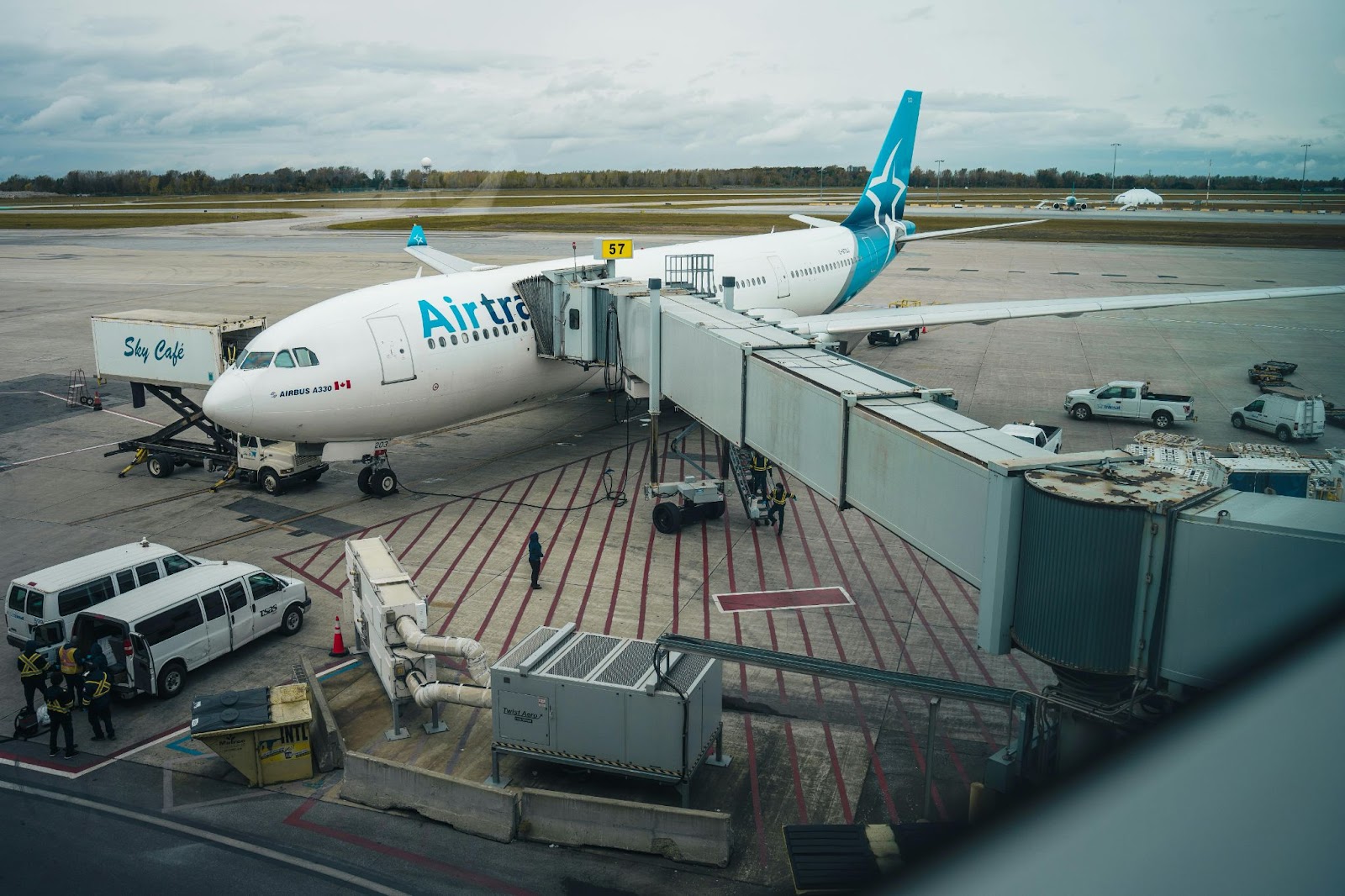
Inventory shrinkage, defined as the loss of aircraft parts, tools, and materials due to theft, fraud, or operational inefficiencies, is a continuous financial and aviation security risk to the industry.
Whether it’s missing engines, unauthorized part removals, or supply chain mismanagement, shrinkage leads to grounded aircraft, disrupted operations, and legal battles.
Recent high-profile cases underscore the severity of the issue. SpiceJet has been accused of removing engines from leased aircraft without permission, while Jet Midwest alleges that Australia’s Rex Airlines stripped and scrapped its aircraft without full payment. Insider threats also play a major role, with aviation employees engaging in smuggling, theft, and fraud due to financial vulnerability.
With airlines and MROs facing rising costs and pressure to streamline operations, tackling inventory shrinkage is more critical than ever. This article explores the causes, financial impact, and best prevention strategies for aviation businesses to mitigate losses and improve accountability.
What causes inventory shrinkage in aviation?
Theft and unauthorized part removal
Aviation assets are incredibly valuable, making them prime targets for inventory theft. One of the most striking recent cases involves SpiceJet, which allegedly removed engines from leased B737-700(BDSF) freighters without approval from Spectre Air Capital. The lessor’s legal team labeled the action as "prima facie theft," accusing the airline of using the engines without payment (CH-Aviation, January 2025).
Similarly, Jet Midwest filed a lawsuit against Rex Airlines, claiming that the carrier stripped four aircraft for parts and scrapped the remaining airframes after failing to complete a $2 million purchase agreement (CH-Aviation, September 2024).
These incidents highlight the risks lessors and MROs face when dealing with financially struggling airlines, and theft isn't just limited to major components like engines.
According to Osprey Flight Solutions, airport and airline employees have been caught smuggling gold, narcotics, and other valuable items using their insider access. Security gaps at MRO facilities, cargo terminals, and aircraft storage sites make it easier for bad actors to exploit aviation assets.
Insider threats and employee exploitation
Insider involvement in aviation shrinkage isn't new, but economic hardships post-pandemic have worsened the problem. A 2021 UK National Crime Agency report warned that airport and airline employees—especially those in security-sensitive roles—were being targeted by organized crime networks due to financial distress (Osprey Flight Solutions, January 2023).
Beyond inventory theft, common schemes include:
- Baggage handlers and cargo workers swapping luggage tags to bypass customs.
- Airline maintenance staff concealing narcotics and contraband inside aircraft electronics bays.
- Ground crew and cleaners smuggling valuable materials like gold hidden in catering carts.
The aviation industry’s reliance on third-party service providers and contractors further complicates oversight, making insider monitoring as challenging as it is essential for reducing shrinkage risks.
The financial impact of inventory shrinkage
Direct financial losses
Inventory shrinkage costs the aviation industry millions annually, but the full financial impact extends beyond the immediate loss of stolen or missing parts.
For example, Jet Midwest is seeking $7.2 million in damages from Rex Airlines after alleging the carrier dismantled and scrapped the aircraft without full payment (CH-Aviation, September 2024).
Beyond these lawsuits, shrinkage leads to:
- Lost revenue from grounded aircraft: When critical components like engines, landing gear, or avionics disappear, aircraft remain out of service, disrupting operations.
- Higher insurance premiums: Frequent claims due to theft or missing parts can drive up costs of theft risk insurance for aviation.
- Penalties and legal fees: Lease violations and disputes over missing assets often result in multi-million-dollar settlements.
Operational disruptions and supply chain issues
Inventory shrinkage doesn’t just hurt balance sheets; it can throw a wrench in international aviation operations.
One McKinsey June 2024 report highlighted that consumer-packaged goods and plastic-and-paper packaging companies are still carrying 15-20% higher inventory levels than pre-COVID-19 averages, while retailers have aggressively cut stock levels to minimize losses.
The aviation industry faces a similar balancing act, as excess inventory can lead to waste, but shortages due to shrinkage cause delays and supply chain bottlenecks.
Operational consequences include:
- Flight cancellations and delays: Missing parts lead to aircraft being classified as AOG (Aircraft on Ground) events, causing costly disruptions.
- Longer maintenance turnaround times: If critical components disappear, maintenance teams must source replacements, increasing downtime.
- Supply chain inefficiencies: Aviation firms must hold larger-than-needed inventories to hedge against theft and fraud risks, tying up capital that could be better allocated elsewhere.
Given these risks, airlines, MROs, and lessors must take proactive measures to track inventory and strengthen aviation security protocols.
Strategies to prevent inventory shrinkage
Implementing advanced tracking and security measures
To prevent the unauthorized removal of high-value components, aviation companies can leverage technology-driven solutions such as:
- RFID and GPS tracking for aircraft parts: These systems enable real-time monitoring of engines, avionics, and other critical inventory.
- Blockchain-based asset tracking: Provides an immutable record of component ownership and transfers, reducing fraud risk.
- AI-powered surveillance at maintenance facilities and storage sites: Helps identify unusual employee behavior, such as unauthorized access to restricted areas.
Several industries already benefit from these technologies, and aviation must follow suit to reduce shrinkage risks.
Strengthening internal controls and audits
Regular audits and inventory reconciliation can significantly reduce shrinkage. Companies should:
- Conduct surprise inspections at maintenance sites and warehouses.
- Limit access to high-value parts with multi-tiered authorization for removal.
- Require dual verification for parts transfers and removals to prevent insider fraud.
Aviation companies should also ensure lease agreements include clear asset protection clauses to prevent disputes like those seen in the Jet Midwest and SpiceJet cases.
Collaboration and industry-wide standards
Enhancing industry cooperation to combat shrinkage
The aviation industry must adopt a collaborative approach to reduce inventory shrinkage, particularly when insider threats and organized crime are involved. The Osprey Flight Solutions report highlighted how aviation employees with financial hardships are being targeted by criminal networks to smuggle drugs, weapons, and valuable aircraft components.
This problem is exacerbated during economic downturns, making employee screening and security training critical.
To address these risks, aviation stakeholders should:
- Share intelligence on theft patterns across airlines, MROs, and law enforcement agencies.
- Standardize reporting procedures for stolen or missing parts to track black-market resale activity.
- Develop global security certifications for aviation employees handling high-value components.
Airports and maintenance facilities must also tighten background checks and establish whistleblower protections to encourage employees to report suspicious activity.
Leveraging technology to strengthen accountability
AI and automation are playing an increasing role in fraud prevention. Industry leaders should invest in:
- AI-powered fraud detection systems that analyze transaction data for anomalies.
- Automated inventory audits using machine learning to flag inconsistencies.
- Secure digital records that create transparent, tamper-proof logs of parts movements.
As seen in the McKinsey June 2024 report, excess inventory can be a liability, but cutting back on stock too aggressively increases vulnerability to supply chain disruptions. AI-driven forecasting models can help balance inventory levels while maintaining security and compliance.
Preventing inventory shrinkage in the aviation industry
Inventory shrinkage is more than an accounting issue—it’s a direct threat to operational efficiency, financial stability, and industry trust. Whether it's airlines accused of stripping leased aircraft, insider threats smuggling valuable components, or supply chain vulnerabilities leading to misplaced inventory, the aviation industry must take proactive steps to mitigate losses.
Key strategies include:
- Strengthening security protocols through RFID tracking, AI surveillance, and blockchain-based asset management.
- Enhancing internal audits and accountability to prevent insider fraud and unauthorized part removals.
- Encouraging industry-wide collaboration to improve reporting and intelligence-sharing on inventory shrinkage trends.
- Leveraging AI and automation to create more accurate inventory management systems and prevent financial losses.
Preventing inventory shrinkage benefits everyone
Inventory shrinkage isn’t just about overcoming your organization’s financial and operational challenges — which are reason enough to tighten security — it’s about protecting the safety of the entire aviation ecosystem.
Strengthening security protocols and improving inventory management protects businesses from financial losses and also safeguards employees, enhances flight with planes using non-stripped, authenticated parts, and contributes to global security.
Companies reducing theft and fraud are protecting their workers—particularly those in lower-wage, high-risk roles—who might otherwise be exploited by criminal networks. More secure and transparent inventory systems ensure that critical aviation parts remain where they belong, preventing costly shortages and eliminating unnecessary stockpiling that drains resources.
Beyond the financial upside, addressing shrinkage also has far-reaching implications for global safety. When aircraft parts are tracked and accounted for, the risk of tampering is reduced, ensuring safer flights. When illicit goods can’t be moved through aviation channels, supply chains remain secure, and illegal activities like drug smuggling become more difficult to execute.
In short, preventing inventory shrinkage extends far beyond protecting engines and avionics parts. From the workers on the ground to the airlines in the sky, every stakeholder benefits from a system that prioritizes accountability, security, and efficiency. The industry's future depends on smarter, more secure inventory practices, and those who invest in them now will reap the rewards in operational stability, cost savings, and long-term trust.