Understanding the financial costs of aircraft maintenance errors and how to minimize them
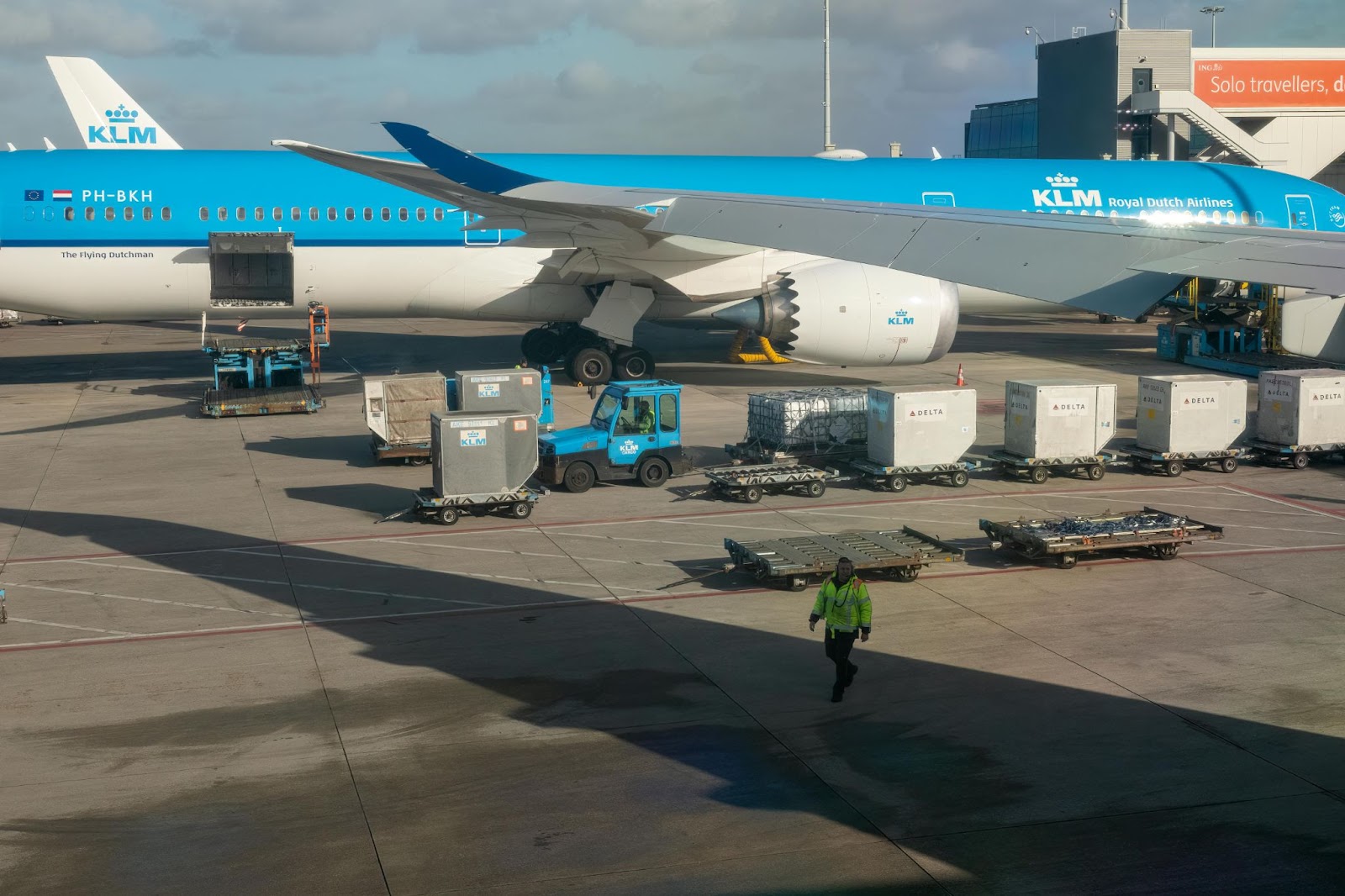
The true cost of aircraft maintenance errors
Aircraft maintenance is a critical part of aviation, overseeing tasks aligned with safety, operational readiness, and compliance. However, when errors arise, they pose major safety risks and come with massive financial consequences.
These costs extend beyond immediate repairs, affecting flight schedules, airline revenue, and even regulatory penalties.
Direct costs: immediate financial impact
Aircraft maintenance errors come with a high price tag, and the financial impact is often immediate. While some expenses, such as regulatory fines, may take time to materialize, the direct costs associated with fixing errors begin accumulating the moment an issue is detected. From unplanned labor to sourcing emergency parts, these costs escalate rapidly.
Repair and replacement costs
When a component is incorrectly installed, damaged during maintenance, or fails prematurely due to human oversight, airlines face significant repair or replacement expenses. This includes shipping fees, supplier markups, and the additional labor required to remove and reinstall the component.
In some cases, a misdiagnosed issue can result in replacing an entire system unnecessarily, adding millions to maintenance budgets.
The total burden also varies depending on aircraft type and part criticality.
A minor interior component failure may only cost a few thousand dollars, but a major mechanical failure—such as damage to an engine, landing gear, or avionics system—can quickly exceed $5 million in replacement costs alone, according to Kevin Michaels of AeroDynamic Advisory. Some parts, such as an engine for a wide-body plane, can easily reach $10 million (CNBC: Airplane engines are in short supply. The business of fixing older ones is booming).
Unplanned labor hours
A single maintenance mistake can trigger a cascading effect, requiring extensive additional labor to diagnose and correct the issue.
Unlike scheduled maintenance, which is generally optimized for efficiency, unplanned repairs derail workflows and demand immediate attention. This often means technicians must work overtime or be pulled from other scheduled tasks, driving up labor costs.
The financial impact is substantial. A study published in Procedia CIRP found that unplanned maintenance costs two to five more (100% to 400% more) than scheduled maintenance (Science Direct: Procedia CIRP). This cost spike is largely due to the need for emergency troubleshooting, additional technician hours, and last-minute procurement of spare parts.
Compounding the issue is the ongoing shortage of highly skilled aircraft maintenance technicians (AMTs), whose high hourly rates reflect major industry demand. When a slip-up forces an AMT to redo work that should have been completed correctly the first time, airlines face not only direct labor costs but also wider system disruptions.
Emergency part procurement expenses
Aircraft maintenance planning typically includes inventory management strategies to safeguard the availability of commonly needed spare parts. However, when a misstep results in an unexpected part failure, airlines often must source replacements on short notice, and that’s where costs spiral out of control.
Expedited shipping fees for Aircraft on Ground (AOG) events vary wildly. Some sources estimate AOG service fees ranging from $100 to $1,000 per shipment (C&L Aviation Group).
Premium expedited transport costs, however, can skyrocket based on distance, urgency, and part size. In worst-case scenarios, an essential part may need to be flown in from overseas, leading to staggering logistics fees that easily exceed the price of the part itself.
The pricing of aviation parts is often volatile—supply chain bottlenecks, low inventory levels, and third-party markups can turn an already expensive repair into a cash sinkhole. The only way for airlines to avoid being at the mercy of such unpredictability is to establish strong relationships with logistics providers and pre-positioning high-priority spare parts at major hubs.
The situation becomes even more problematic with legacy aircraft models, where replacement components aren’t just expensive—they’re scarce. When no parts are immediately available, airlines face the worst possible scenario: extended aircraft downtime, potential flight cancellations, and loss of revenue that far exceeds the cost of the part itself.
Indirect costs: Hidden financial toll
Beyond direct costs, maintenance errors create long-term financial damage that can cripple air travel. From delays and passenger compensation to regulatory fines and reputational harm, the ripple effects extend far beyond any initial mechanical mistake.
AOG losses
When an aircraft is unexpectedly grounded due to a maintenance oversight, airlines lose revenue while still incurring operating expenses. For airlines, AOG events and other flight delays eat up $60 billion in annual global revenue—roughly 8% of airline revenue pre-COVID (Wipro). The longer an aircraft remains out of service, the greater the setbacks across an airline’s flight network.
For AOG-specific incidents, the cost can range from $10,000 to $150,000 per hour (AAA Air Support).
Passenger compensation and rebooking expenses
AOG events often lead to canceled flights, forcing airlines to rebook passengers or issue refunds, sometimes at premium last-minute fares.
Consumer protection laws can also require cash compensation, hotel accommodations, and meal vouchers for stranded travelers. For airlines operating full flights, these expenses quickly mount and often exceed the cost of the maintenance fix itself.
Specific passenger compensation figures are scarce, but the monetary implications are substantial. For instance, the Government Accountability Office (GAO) reported that from July 2021 through April 2022, flight cancellations potentially affected over 15 million passengers, and delays impacted over 116 million passengers (GAO: Airline Passenger Protections). Given these numbers, even modest per-passenger expenses can accumulate significantly.
And the majority of these delays—a staggering 60%—were airline-caused, underscoring the importance of minimizing aircraft maintenance errors (Department of Transportation).
Regulatory fines and legal liability
Regulatory bodies impose heavy penalties for maintenance mistakes, particularly when procedures are not followed. Failure to follow procedures (FFP) accounts for 40.5%–87% of maintenance-related events (FAA), and non-compliance can result in fines, audits, and lawsuits. If an incident escalates to a safety violation, the fines can increase exponentially.
Reputational damage
Frequent maintenance delays or high-profile failures erode passenger trust and push travelers toward more reliable competitors. The damage isn’t just theoretical—customer perception takes a measurable hit when delays occur, especially when communication fails.
A Bain & Company study found that a customer’s Net Promoter Score (NPS) drops by 16 points if their flight is delayed. If passengers feel uninformed, the drop skyrockets to 90 points, showing how poor communication compounds the damage (Bain & Company: How US Airlines Can Soar Above Summer Travel Frustrations).
Beyond lost bookings, reputational harm can lead to higher insurance premiums, trouble securing aircraft leases, and weakened corporate partnerships.
Airlines with frequent AOG-related delays risk long-term revenue loss, as passengers and business clients take their loyalty elsewhere. Even one high-profile maintenance failure can have lasting effects, making proactive error prevention essential.
The good news is that most maintenance missteps are preventable. Since human factors and procedural failures drive the majority of maintenance-related incidents, companies have a clear opportunity to reduce accidental blunders through better training, process standardization, and AI-driven predictive maintenance.
But first, it’s crucial to understand why these mistakes happen in the first place—and how seemingly small lapses in judgment can escalate into costly failures.
Human factors and the role of maintenance errors
While technology and automation have improved aviation safety, human factors remain the leading cause of maintenance slip-ups.
For example, it’s estimated that human distraction alone accounts for 15% of all maintenance mishaps (FAA Aircraft Maintenance Technician Handbook).
Distraction on the job is one of 12 preventable, human-related factors for maintenance errors known as the “Dirty Dozen.” (FAA: Avoid the Dirty Dozen). Incredibly, 80% of all maintenance mistakes involve “Dirty Dozen” human factors.
The “Dirty Dozen” — A breakdown of costly human errors
- Lack of communication: Poor communication between technicians leads to misinterpretations, incorrect installations, and skipped procedures.
- Distraction: A simple interruption during maintenance work can cause fundamental steps to be overlooked.
- Fatigue: Fatigue-related errors impair focus, memory, and decision-making, increasing the risk of mistakes and loss of situational awareness. The risk worsens with long shifts, inconsistent procedures, and fatigued coworkers.
- Pressure: Tight turnaround times increase procedural deviations, leading to costly mistakes.
- Complacency: Technicians performing routine tasks may assume procedures are correct without verifying, increasing error rates.
- Lack of knowledge: Aircraft systems evolve rapidly; outdated training can result in improper maintenance.
- Lack of awareness: Failure to understand how one action impacts the entire aircraft system can cause major failures.
- Lack of process: Technicians may follow informal workarounds rather than official procedures, increasing risk.
Real-world examples of “Dirty Dozen” aircraft maintenance errors
Incorrect engine component installation in Hong Kong (2021)
In July 2021, a UPS Boeing 747-8 freighter experienced an engine fire shortly after takeoff from Hong Kong International Airport. According to the official incident report, the fire resulted from an improperly installed component, specifically a loose valve fitting that caused a significant fuel leak. This maintenance oversight triggered substantial costs from emergency procedures, engine repairs, and broader company disruptions.
Loose chip detector leads to engine failure in Ireland (2022)
In April 2022, a Boeing 767-300 en route south of Cork, Ireland, suffered a loss of oil pressure in its left engine, prompting an emergency diversion to Shannon Airport. The cause was identified as an incorrectly reinstalled chip detector during routine maintenance, leading to an oil leak and engine shutdown. This mishap underscores the vital importance of adhering to proper maintenance procedures (Air Accident Investigation Unit Ireland Synoptic Report).
Boeing 737 door plug failure in Oregon, USA (2024)
In January 2024, the FAA grounded 171 Boeing 737-9 MAX aircraft after a cabin door plug blew out mid-flight on Alaska Airlines Flight 1282 (FAA Newsroom).
According to the FAA incident reports and subsequent audits, this failure resulted from systemic manufacturing and quality-control deficiencies at Boeing and its subcontractor, Spirit AeroSystems.
The revenue and operational repercussions were substantial, including halted production expansion, intensive FAA oversight, mandated inspections, and ongoing investigations.
This incident underscores the costly impact of maintenance and manufacturing errors and highlights the importance of rigorous safety checks at every stage of production, installation, and maintenance.
Aircraft operators and manufacturers alike must prioritize continuous quality monitoring, rigorous training, and transparent safety cultures to prevent similarly compromising incidents.
How to minimize aviation maintenance errors and reduce costs
AI-powered predictive maintenance: The future of error prevention
Minimizing aviation maintenance errors requires integrating advanced technology, enforcing procedural discipline, and leveraging predictive maintenance powered by artificial intelligence.
AI-driven maintenance solutions are rapidly transforming the industry, allowing airlines to anticipate issues before they occur, dramatically reducing Aircraft on Ground (AOG) events, and optimizing overall operational agility.
Real-time data enables the early detection of anomalies for potential component failures. According to one Deloitte study, predictive maintenance strategies can reduce facility downtime by up to 30% and lower equipment costs by 15% (Deloitte).
Delta Air Lines exemplifies this proactive, AI-driven approach, achieving a 95% success rate in predicting mechanical issues, which has dramatically reduced maintenance-related flight cancellations (Delta Tech Ops).
Standardized processes and compliance enforcement
Procedural compliance is crucial to reducing human mistakes, which account for approximately 42.5% of all Procedure Change Requests (PCRs). That figure underscores the need for clear, consistent, and enforced documentation (FAA).
Airlines can significantly reduce documentation inaccuracies and improve the reliability of maintenance records by implementing standardized checklists and digital logbooks.
Training and certification: The key to aviation error reduction
Continuous education and certification for technicians are vital. As aircraft systems evolve, ongoing training helps ensure technicians remain updated on best practices and emerging technologies. Frequent procedural audits reinforce compliance, reducing the likelihood of costly mistakes due to procedural deviations.
AOG support strategies: Minimizing downtime costs
Adopting an effective Aircraft on Ground (AOG) workflow can significantly cut costs. Pre-positioning essential parts at key hubs reduces response times, while AI-based remote troubleshooting helps quickly diagnose and fix issues.
Predictive analytics further boosts savings by catching problems before they become serious. Airlines embracing this predictive approach can reduce business expenses by up to 20%, according to a University of Maryland study (Avia Solutions Group).
Final thoughts: Investing in prevention saves millions
From direct repair costs to regulatory penalties and reputational damage, the financial burden of AOG aviation issues is staggering.
Investing in AI-powered predictive maintenance, standardized compliance, and rigorous training programs allows aviation stakeholders to reduce maintenance costs, improve safety, and enhance operational performance.
The industry’s future depends on proactive maintenance solutions—and the companies that prioritize technology-driven error prevention will ultimately save millions, protect passenger trust, and strengthen safety for a brighter, more resilient future.