Using Historical Data to Predict Aviation Supply Chain Disruptions
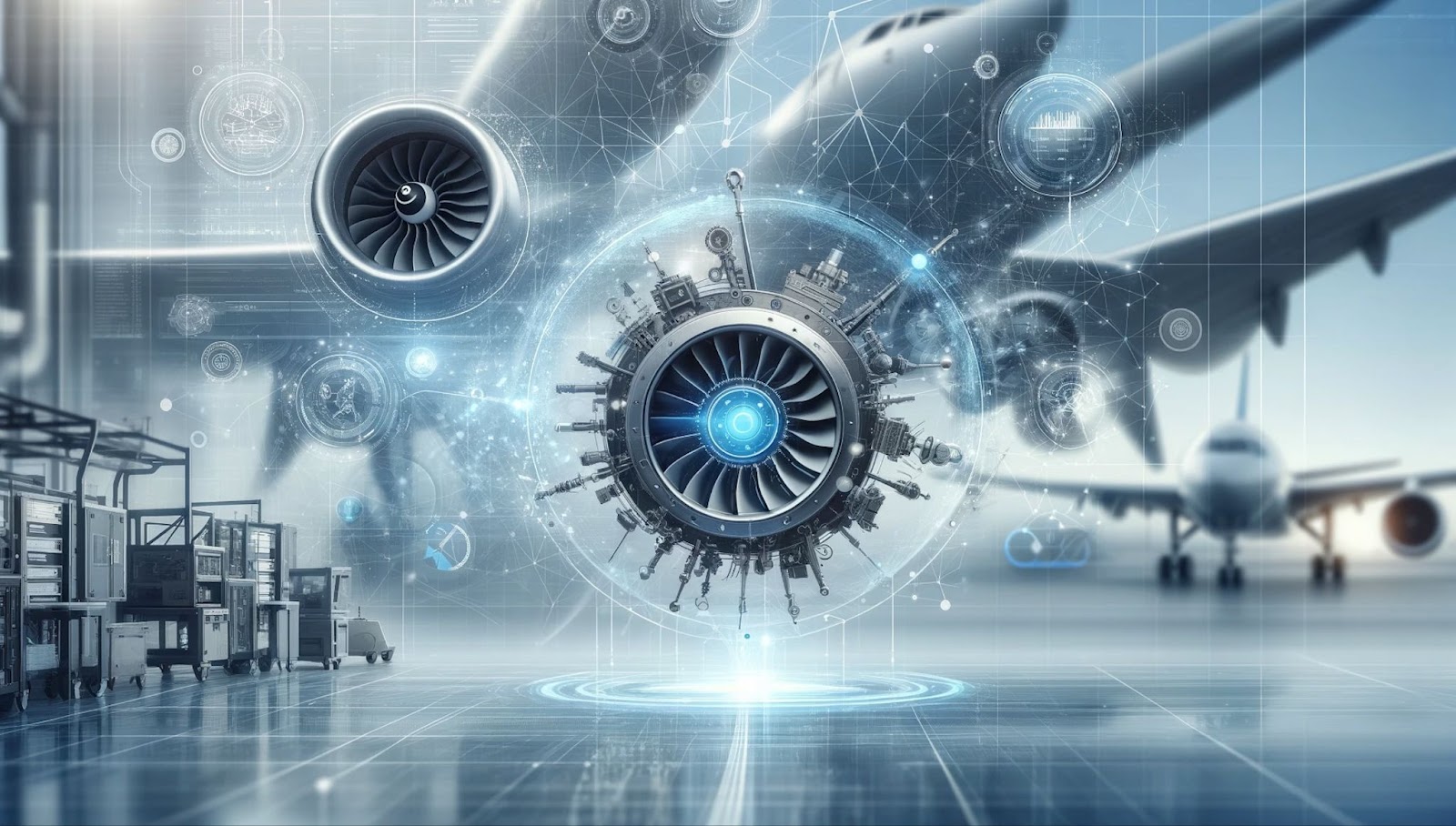
Every airline has been there—waiting for a critical part that’s stuck in transit or delayed by a supplier, with aircraft grounded and schedules upended. For aviation companies, these disruptions aren’t just an inconvenience: they impact revenue, customer trust, and operational efficiency.
Supply chain issues in aviation don’t always have simple solutions, but there is a smarter way to manage them. Leveraging historical data means you can anticipate supply chain disruptions well before they unfold. With the power to see trends, spot risks, and make proactive adjustments, predictive maintenance transforms supply chain management from a guessing game into a strategic advantage.
This article explores how data insights can help everyone involved in the aviation supply chain work toward a shared goal: keeping planes in the air and operations running smoothly, no matter the challenges ahead.
Aviation supply chain management
Logistics are exceptionally complex in the global aviation industry, with every step—from sourcing to delivery—crucial to keeping aircraft operational and on schedule.
-Efficient supply chain management (SCM) in aviation requires integrating the key domains identified in leading models, such as Gartner’s supply chain framework: planning, sourcing, making, delivering, and returning.
Planning involves forecasting demand and aligning resources to ensure operational readiness while sourcing emphasizes vendor selection, procurement strategies, and contract management to secure critical parts.
The “make” phase, though less prominent in aviation, includes maintenance, repair, and overhaul (MRO) activities, ensuring parts and components are ready for deployment. Delivery focuses on logistics optimization—streamlining transportation and ensuring timely delivery of parts and components to minimize downtime.
Finally, the return process includes the recycling, refurbishing, or disposal of unserviceable parts to maintain sustainability and compliance with environmental regulations.
In addition to these core areas, aviation SCM must address cross-cutting functions like inventory management, workforce planning, and real-time data analytics. When balancing these interconnected components, aviation companies can maintain schedule integrity, adapt to disruptions, and meet the industry’s stringent safety and compliance standards.
Unique supply chain challenges in Aviation:
- Multiple stakeholders: Aviation SCM involves coordination across a broad network, from manufacturers to MRO providers, each playing a critical role in keeping aircraft flight-ready.
- Dependence on specialized parts: Timely delivery of essential, often scarce, parts is vital. From large components like engines to smaller but crucial items like sensors, every part must arrive precisely when needed to avoid grounding aircraft.
- Cascading effect of delays: A single delay can create a domino effect, impacting the entire supply chain. Even minor setbacks in one area can lead to significant delays across downstream supply chain processes.
Common disruptors in aviation supply chains
Aviation supply chains face a complex landscape of potential setbacks. A minor delay can escalate, disrupting operations and impacting schedules. Here are a few common disruptors that historical data can help manage:
- Supplier delays and demand spikes: Sudden spikes in demand or delays from suppliers can lead to critical shortages, especially for high-demand or limited-supply parts.
- Regulatory setbacks: Complex aviation regulations often require specific approvals or certifications. If these processes are held up, they can hold up entire operations—a persistent challenge in a tightly regulated industry.
- Regional disruptions: Natural disasters or local events can block shipping routes or restrict access to key parts, impacting the entire supply chain. Or they could disrupt maintenance schedules requiring planes to be serviced elsewhere at short notice.
Beyond these, factors like international tariffs, shifting trade policies, material shortages, or labor strikes introduce additional layers of uncertainty. While some of these may not be predictable with historical data alone, they highlight the importance of a flexible, proactive approach to aviation supply chain management.
By analyzing historical trends, aviation companies can still anticipate many risks, helping them create buffer strategies for more resilient operations.
Using historical data to prevent supply chain disruptions
Historical data provides insights into recurring patterns and potential issues that affect supply chain functions. Through examining previous hiccups—such as supplier delays, fluctuations in part demand, or seasonal supply bottlenecks—aviation companies can uncover future risks.
With these insights, airlines and MRO providers can prepare for and address issues instead of waiting for them to impact operations.
Key applications of aviation data analytics:
- Demand forecasting: With continual access to historical trends, aviation companies can forecast demand for parts more accurately for optimal inventory levels and minimized risk of stockouts. They can even automate procurement when levels fall below PAR.
- Supplier performance evaluation: Analyzing past supplier performance enables companies to identify reliable vendors for quality and on-time parts delivery, and plan for lead times and expected delays.
- Seasonal pattern identification: Some supply chain challenges are seasonal, such as increased parts demand during peak travel times. Understanding these patterns helps aviation companies adjust inventory levels and procurement schedules, avoiding delays and ensuring smooth operations during high-demand periods.
Predictive analytics builds on historical data to identify supply chain risks
While historical data helps identify past issues, predictive analytics goes a step further by using that data to forecast potential disruptions before they happen.
To an extent, analysts can look at historical data to plan for future events. But predictive analytics applies advanced machine-learning (ML) algorithms to historical records, enabling more pinpoint accuracy so aviation companies can make proactive adjustments with greater confidence that these measures are justified.
Here’s how predictive analytics works in a supply chain context:
- Data collection: Predictive systems gather historical data from various sources, including inventory management systems, asset management systems, and supplier databases. Combined, this data forms an extensive comprehensive record that predictive algorithms can analyze in split seconds.
- Trend analysis: Through machine learning, predictive software identifies recurring sequences in lead times, peak demand, and supplier rate of on-time performance. For instance, the system might detect that Supplier A is your worst performer in the summer months but your top performer in the winter and early spring. Without these insights, you might have cut Supplier A altogether, significantly upping operating costs for 25% of the year.
- Risk assessment: The software flags high-risk suppliers, parts, and geographic regions. This assessment empowers aviation companies to make informed decisions about when to reorder parts or source from alternative vendors, and when and where to adjust flight schedules.
These actionable insights are making a meaningful difference for aviation businesses today.
Real-world examples of predictive insights in aviation supply chains
Here are a few real-world applications of how companies have used historical data to prevent aviation supply chain disruptions.
Delta Air Lines
With over 95% accuracy in predicting potential failures, Delta’s predictive maintenance program sets a new standard for reliability. Its predictive maintenance uses both historical data and a continual influx of real-time data from IoT sensors on critical components to maximize MRO efficiency.
Alaska Airlines
AI systems, like Alaska Airlines' Flyways, optimize flight routes on the go. Through analyzing weather, aircraft weight, planned paths, and other historical data, Flyways technology finds the most efficient course. In just six months, Flyways saved 480,000 gallons of fuel (for an estimated savings of around $3 million) and cut 4,600 tons of carbon emissions.
These examples show how predictive analytics, backed by historical data, is helping aviation companies run smoother, cut costs, and keep their fleets ready to fly.
Strategic advantages of using historical data for aviation supply chains
For aviation companies, the power of historical data goes beyond identifying individual issues—it provides a foundation for a more resilient supply chain and loyal customer base.
Maximized fleet availability
Predictive insights minimize unexpected delays and shortages, keeping aircraft ready for scheduled flights and reducing costly downtime. Through ensuring parts are available when needed, airlines can maintain higher operational availability and meet passenger demand more reliably —crucial when 40% of air passengers in the U.S. have a connecting flight. That figure is expected to rise to 45% by 2030.
Airlines using historical data plus AI to keep planes operational are poised to capture more market share from airlines that rely on dated methods to predict (guess at) future supply chain performance.
Cost savings
Historical data, continually updated and expertly analyzed, means better equipment maintenance and flight optimization, which can reduce fuel costs. With fuel being a huge component of any carrier’s annual budget, even a 1% reduction means savings of several million dollars.
Optimized passenger loads
Effective supply chain management can help airlines consistently maintain high load factors, targeting 85% or better. Timely aircraft maintenance ensures all parts are available in good working order when needed, minimizing flight cancellations and keeping more aircraft operational. This allows for more consistent, reliable scheduling.
Delta Air Lines, as one noted example, reduced its maintenance-related flight cancellations from 5,600 in 2010 to a staggering 55 in 2018—just by using historical data to implement better predictive maintenance strategies. That’s a 99.1% reduction in flights canceled due to MRO issues.
While this success is remarkable, many aviation companies have yet to adopt similar strategies. For every airline taking proactive steps like Delta, two others continue to rely on outdated methods, leaving money on the table, hurting profitability, and risking their reputations. Embracing data-driven insights, airlines can stay ahead of the curve and reap the benefits of a more resilient, efficient supply chain.
Stronger, more reliable partnerships
Analyzing historical performance allows companies to prioritize vendors with proven quality and reliability, creating a stable supply chain. This stability builds trust—from air fleets relying on dependable providers to passengers and freight customers trusting airlines to deliver consistently.
Achieving supply chain resilience with ePlaneAI
In aviation, supply chain resilience is critical. ePlaneAI’s automated inventory management platform delivers real-time monitoring and predictive insights to keep operations running smoothly. Here’s how:
- Real-time alerts: ePlaneAI continuously tracks key supply indicators, alerting teams to risks like stock shortages, supplier issues, or delivery delays, so minor disruptions are managed before they escalate.
- Reliable vendor selection: Analyzing historical supplier data, ePlaneAI flags reliable vendors and those with inconsistent performance, helping companies secure dependable partnerships and minimize risk.
- Accurate demand forecasting: ePlaneAI’s predictive algorithms improve demand forecasts, preventing overstocking, stockouts, and unnecessary storage costs while ensuring aircraft grounding is avoided.
- Dynamic inventory optimization: The platform adapts inventory levels dynamically based on real-time usage data, seasonal patterns, and anticipated demand, ensuring the right parts are always available when needed.
- Seamless integrations: ePlaneAI connects with existing ERP, MRO, and supply chain systems, enabling a unified workflow and eliminating the need for manual data transfers or redundant processes.
- Risk mitigation insights: The platform identifies high-risk suppliers, parts, and locations, empowering teams to act proactively and minimize the impact of potential supply chain disruptions.
- Data-driven decisions: Comprehensive supply chain insights empower aviation companies to make fast, strategic choices that keep fleets operational and competitive.
ePlaneAI uses historical data to see patterns and predict needs, and real-time data to tackle issues as they come. Together, they keep your supply chain steady and your aircraft in the air.
Final thoughts
In aviation, timing and reliability are everything. Predicting supply chain disruptions with data is a must, to stay relevant in a world increasingly powered by AI.
Through partnering with ePlaneAI, companies can turn historical data into proactive strategies—reducing downtime, lowering costs, and boosting fleet readiness. A predictive approach means staying resilient, efficient, and prepared for challenges.
Ready to move beyond reactive maintenance and last-minute fixes? Whether you manage fleets, supply parts, or oversee aviation logistics, ePlaneAI can help transform your historical data into a predictive powerhouse. Streamline operations, improve efficiency, and keep the entire supply chain running smoothly—no matter what’s ahead.